D7 cold-work tool steel is a high-carbon, high-chromium air-hardening tool steel that exhibits exceptional wear resistance. The high carbon and vanadium contents result in numerous, hard vanadium carbide particles in the steel. These carbides exhibit a hardness that is equivalent to approximately 80 to 85 Rockwell C
» USA: AISI D7
» Europe: X220CrVMo13-4
» Japan: JIS SKD7
» Germany: 1.2380
» UK: BS BD7
CHEMICAL COMPOSITION
C | Cr | SI | Mn | Mo | V | P | S | |
Min | 2.15 | 11.50 | 0.10 | 0.10 | 0.70 | 3.80 | -- | -- |
Typical | 2.30 | 12.50 | 0.35 | 0.35 | 0.95 | 4.10 | -- | -- |
Max | 2.50 | 13.50 | 0.60 | 0.60 | 1.20 | 4.40 | 0.035 | 0.035 |
APPLICATIONS
- » Brick mold liners
- » Flattening Rolls
- » Briquetting Dies
- » Powder compaction Tooling
- » Deep drawing Dies
- » Machine Tool ways
FORM SUPPLIED
- » Coil
- » Steel strips
- » Sheets
- » Flat bars
- » Plates
- » Tubes
- » Round bars
- » Seamless pipes
Available surface conditions : hot rolled, ground, peeled, turned, drawn, cold rolled
HEAT TREATMENT
- Annealing : Heat slowly to 1600° F – 1650° F, and hold for uniformity, furnace cool at a rate of 20° F per hour to 1000° F then air cool. Expect Brinell hardness
235 – 262 - Hardening : Preheat to 1500° F and soak until uniformly heated and either transfer or raise furnace temperature to 1850° F 1950° F, and hold 1 hour per inch of greatest thickness. Cool in still air.
- Forging/Rolling: Preheat to 1500° F and soak thoroughly. Then raise to 2050° F – 2125° F. Do not forge or roll below 1800° F, cool slowly from the forging or rolling temperature. Do not normalize.
- Tempering : Temper immediately after quenching, before part has cooled to below 150° F. Parts should be held a minimum of 2 hours per inch of greatest
thickness. Double tempering is recommended. For maximum wear resistance temper at 300° F. The above tempering table may be used as a guide. However, since 1/2”dia. specimens were used for this test, it may be found that heavier sections are several points lower.
Tool | Hardening | Tempering |
single edge cutting tools | 1220 ºC | 550-570 ºC |
multi edge cutting tools | 1180-1220 ºC | 550-570 ºC |
cold work tools | 1050-1150 ºC | 550-570 ºC |
PROCESSING
D7 can be worked as follows :
- Machining( grinding, turning, milling)
- Polishing
- Hot forming
- Electrical discharge machining
- Welding(special procedure incl. pre-heating & filler
materials of base material composition)
GRINDING
During Grinding, local heating of the surface, which can alter the temper, must be avoided. Grinding wheel manufacturers can provide advise on the choice of grinding wheels
SURFACE TREATMENT
The Steel Grade is a perfect substrate material for PVD coating. If nitriding is requested, a small diffusion zone is recommended but avoid compound and oxidized layers.
DELIVERY HARDNESS
- » Typical soft annealed hardness is 260 HB
- » Cold drawn and cold rolled material is typically 10-40 HB harder
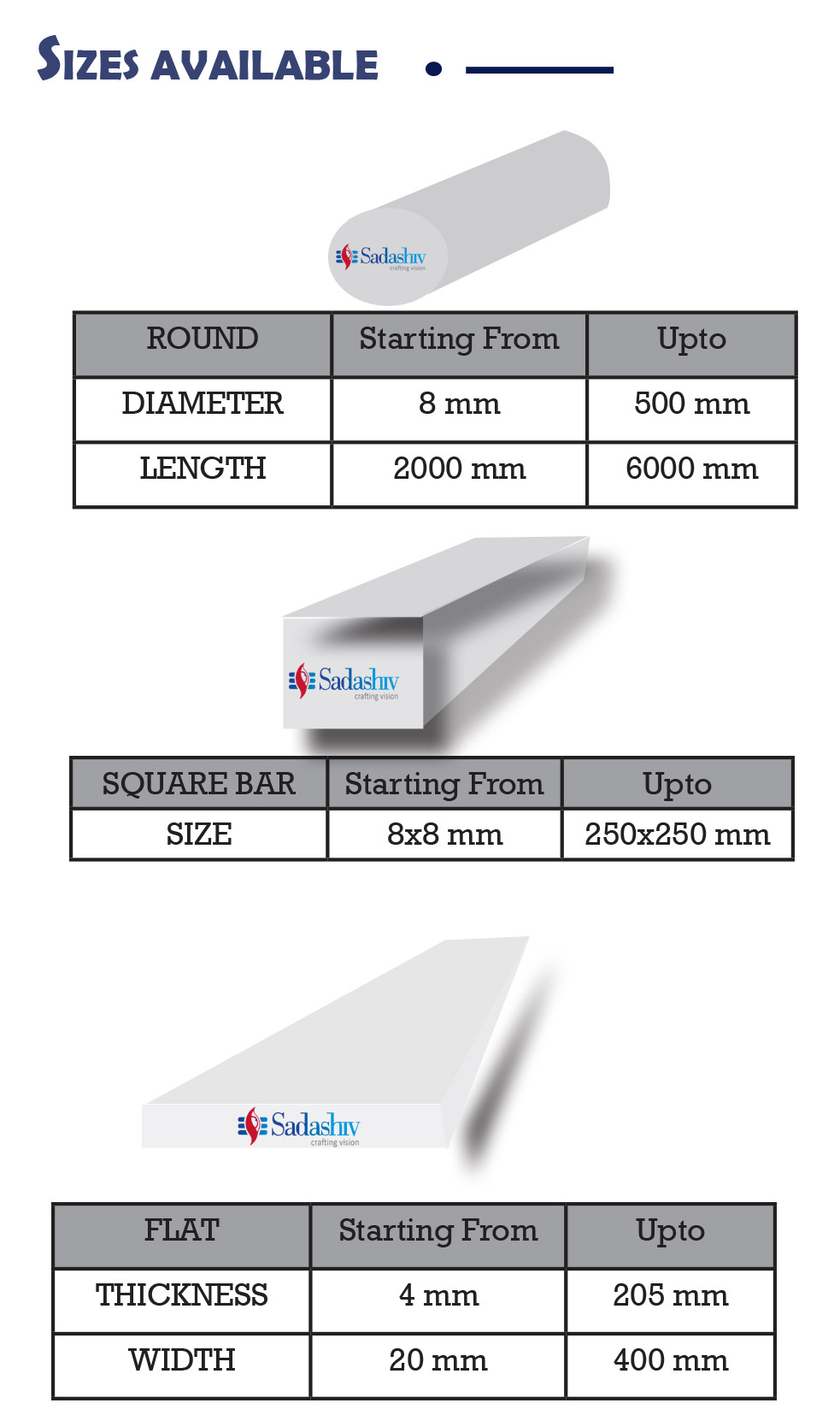
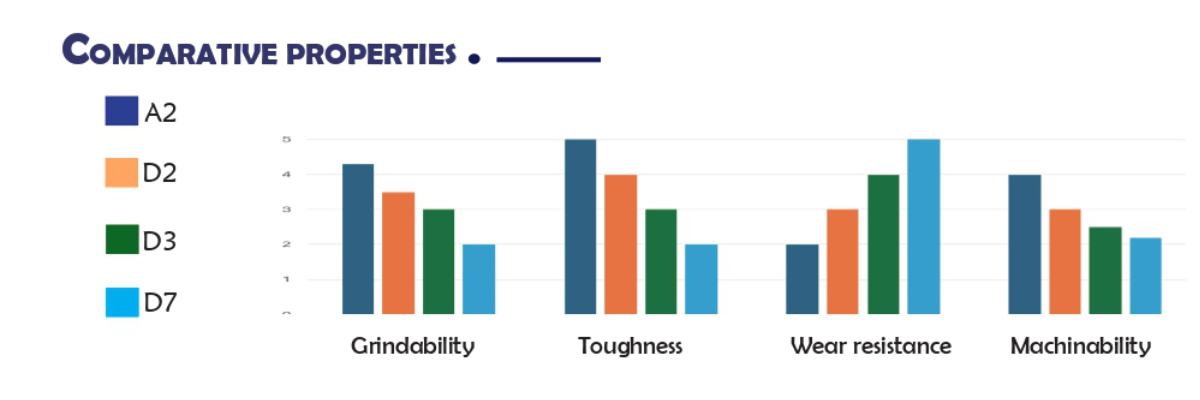