DB6 is highly recommendable for Close Die Forgings due to its characteristics of high wear-resistance, extra toughness , high hardness which is achieved with Cr-Ni-Mo-V high graded alloys. DB6 Steel is a tool steel grade that comes under the DIN EN ISO 4957 standard. Due to its excellent combination of wear resistance, additional toughness, and high hardness which are attained using Cr-Ni-Mo-V high graded alloys, DB6 Steel is highly recommended for Close Die Forgings.
» USA: AISI L6
» France: AFNOR 55NCDW7
» Germany: 1.2714
» Europe: 55NiCrMoV
C | Cr | SI | Mn | Mo | V | Ni | P | S | |
Min | 0.50 | 1.00 | 0.10 | 0.65 | 0.45 | 0.07 | 1.50 | -- | -- |
Typical | 0.55 | 1.10 | 0.25 | 0.80 | 0.50 | 0.095 | 1.65 | ||
Max | 0.60 | 1.20 | 0.40 | 0.95 | 0.55 | 0.12 | 1.80 | 0.035 | 0.035 |
APPLICATIONS
- » Dies
- » Moulds
- » Tools
- » Bearings
- » Rolls
- » Blades
- » Piston Rods
- » Punches
FORM SUPPLIED
- » Round bar
- » Sheets
- » Hexagonal Bar
- » Square Block
- » Flat
Available surface conditions : hot rolled, ground, peeled, turned, drawn, cold rolled
HEAT TREATMENT
- Stress-releiving : Heat the component to 600–650°C, soak for two hours per 25 mm of section, and cool to 500°C in a boiler.
- Annealing : Soak Thoroughly at 740-760 °C before furnace cooling at a maximum rate of 10 °C per hour down to 600 °C followed by cooling in air.
- Hardening: Preheat to 650°C, then quickly raise the temperature to 900–950°C and quench in oil.
- Forging: Gradually warm up to 700°C, then quickly raise the temperature to 1050°C. Keep forging over 800°C, then slowly cool in a furnace or vermiculite.
Tool | Hardening | Tempering |
single edge cutting tools | 1220 ºC | 550-570 ºC |
multi edge cutting tools | 1180-1220 ºC | 550-570 ºC |
cold work tools | 1050-1150 ºC | 550-570 ºC |
PROCESSING
DB6 can be worked as follows :
- Machining( grinding,turning,milling)
- Polishing
- Hot forming
- Electrical discharge machining
- Welding(special procedure incl. pre-heating & filler
materials of base material composition)
GRINDING
During Grinding, local heating of the surface, which can alter the temper, must be avoided. Grinding wheel manufacturers can provide advise on the choice of grinding wheels
SURFACE TREATMENT
The Steel Grade is a perfect substrate material for PVD coating. If nitriding is requested, a small diffusion zone is recommended but avoid compound and oxidized layers.
DELIVERY HARDNESS
- » Typical soft annealed hardness is 360-430 BHN
- » Cold drawn and cold rolled material is typically 10-40 HB harder
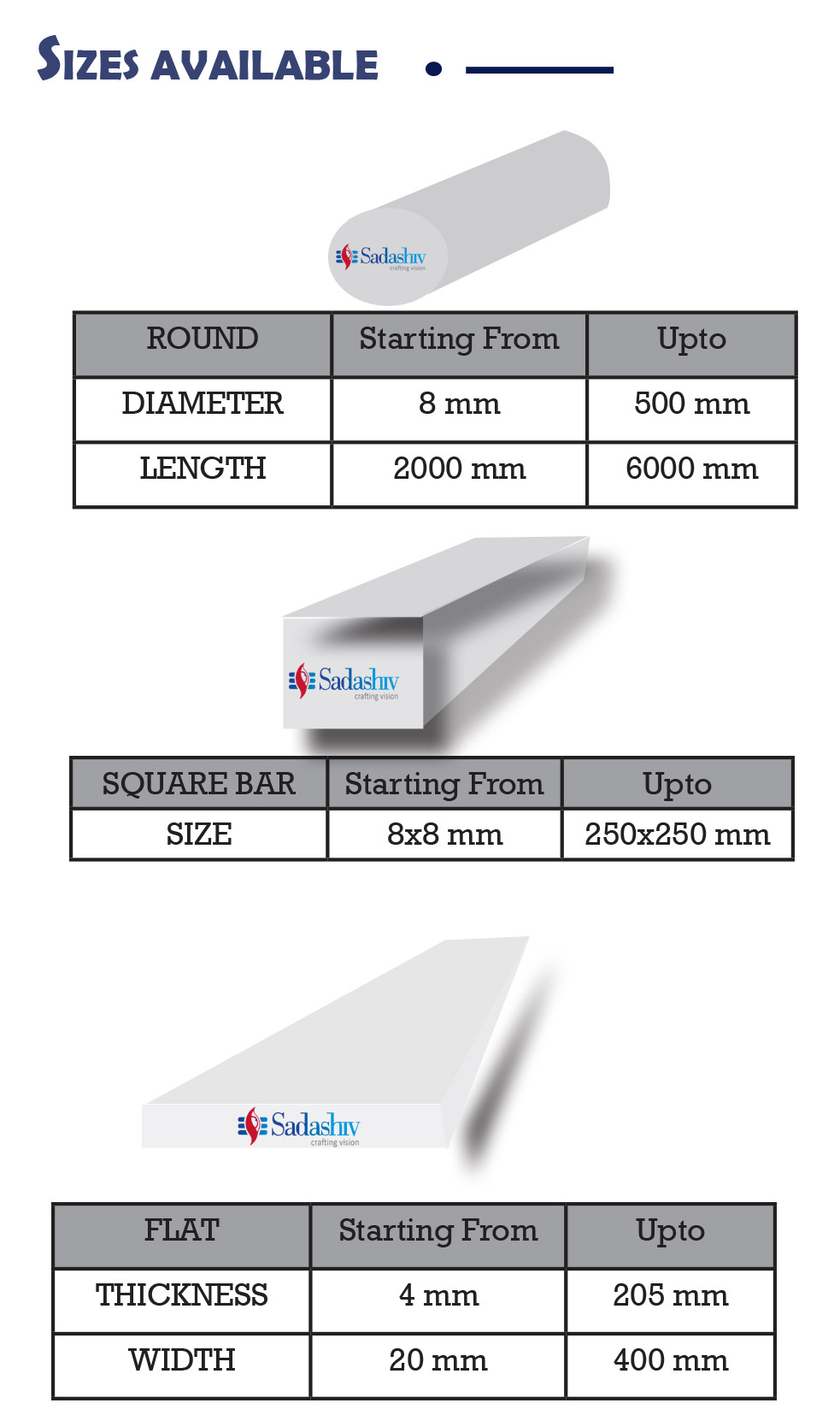
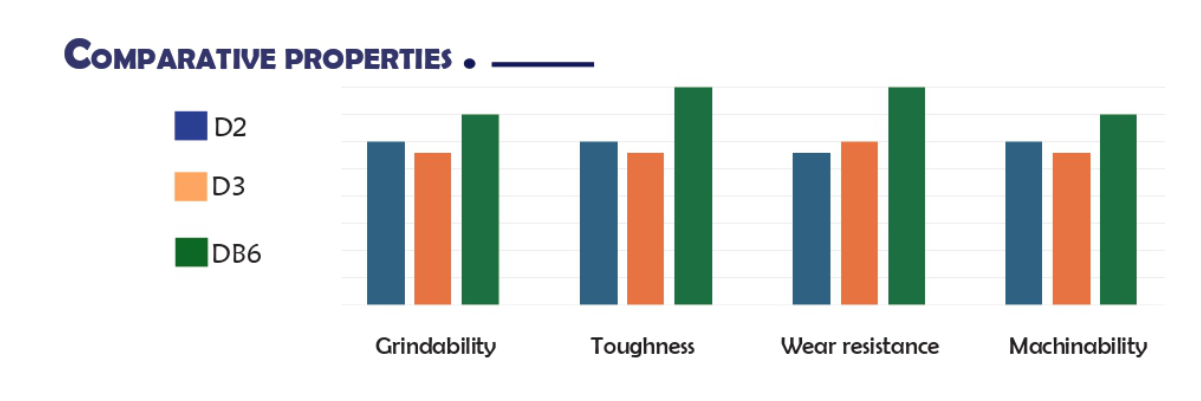