AISI A2 Tool Steel is one of ‘A’ group cold works steel in ASTM A681 standard. A2 Tool Steel is a versatile, air hardening chromium alloy tool steel that replaces O1 tool steel when safer hardening, less distortion and increased wear resistance are required.
» USA: AISI A2
» France: AFNORZ100CDV5
» Japan: JIS SKD12
» Europe: X100CrMoV5
» Germany: 1.2363
» UK: BA2
C | Cr | SI | Mn | Mo | V | P | S | |
Min | 0.95 | 4.75 | 0.10 | 0.40 | 0.90 | 0.15 | -- | -- |
Typical | 1.00 | 5.10 | 0.30 | 0.70 | 1.15 | 0.30 | -- | -- |
Max | 1.05 | 5.50 | 0.50 | 0.40 | 1.40 | 0.50 | 0.035 | 0.035 |
APPLICATIONS
- » Blanking Dies
- » Forming Dies
- » Reamers
- » Mandrels
- » Cold shears
- » Shear and slitter blades
- » Threading Tapes
- » Punches & punch plates
FORM SUPPLIED
- » Round bar
- » Flat Bar
- » Drill Rod
- » Plates
- » Square Block
Available surface conditions : hot rolled, ground, peeled, turned, drawn, cold rolled
HEAT TREATMENT
- Stress-releiving : After heavy grinding or machine it is advisable to stress relieve tool steel A2 to reduce the danger of cracking or distortion during subsequent heat treatments. Heat slowly to 670-700°C, soak for a minimum of two hours per 25mm of section then cool down in the furnace
- Annealing: To anneal A2 tool steel for lowest hardness, heat slowly to 899°C(1650°F) and hold at this temperature for about two hours per inch of greatest cross-section. Cool steel A2 at a rate of 20°F (10°C) per hour to 650°C (1200°F)and reheat to 732°C (1350°F); hold 3 hours per inch of greatest cross-section; furnace cool at 20 degrees per hour to 593°C (1100°F); then furnace-cool to 482°C (900°F) and air-cool.
- Hardening: Preheating temperature: 1200–1380°F (650–750°C). Austenitizing temperature: 1700 –1780°F (925–970°C) but usually 1720–1760°F (940–960°C).
- Quenching : Martempering bath or uidized bed at 360–430°F (180–220°C) or 840–1020°F (450–550°C) then cool in air
--Circulating air or atmosphere
--Vacuum furnace with overpressure of gas at cool
--Oil (only for small and uncomplicated tools) - Tempering : Choose the tempering temperature according to the hardness required by reference to the tempering graph. Heat uniformly and thoroughly to the desired temperature and hold for 25 minutes per cm of thickness. Tool steel A2 can be double tempering, after intermediate cooling to room temperature. Temper at 200°C for a balance of hardness and strength or 350°C where strength is more important than hardness. A minimum holding time of 2 hours per inch of greatest cross-section should be used.
Tool | Hardening | Tempering |
single edge cutting tools | 1220 ºC | 560 ºC |
multi edge cutting tools | 1180-1220 ºC | 560 ºC |
cold work tools | 1050-1150 ºC | 560 ºC |
PROCESSING
A2 can be worked as follows :
- Machining( grinding,turning,milling)
- Polishing
- Hot forming
- Electrical discharge machining
- Welding(special procedure incl. pre-heating & filler
materials of base material composition)
GRINDING
During Grinding, local heating of the surface, which can alter the temper, must be avoided. Grinding wheel manufacturers can provide advise on the choice of grinding wheels
SURFACE TREATMENT
The Steel Grade is a perfect substrate material for PVD coating. If nitriding is requested, a small diffusion zone is recommended but avoid compound and oxidized layers.
DELIVERY HARDNESS
- » Typical soft annealed hardness is 250 HB
- » Cold drawn and cold rolled material is typically 10-40 HB harder
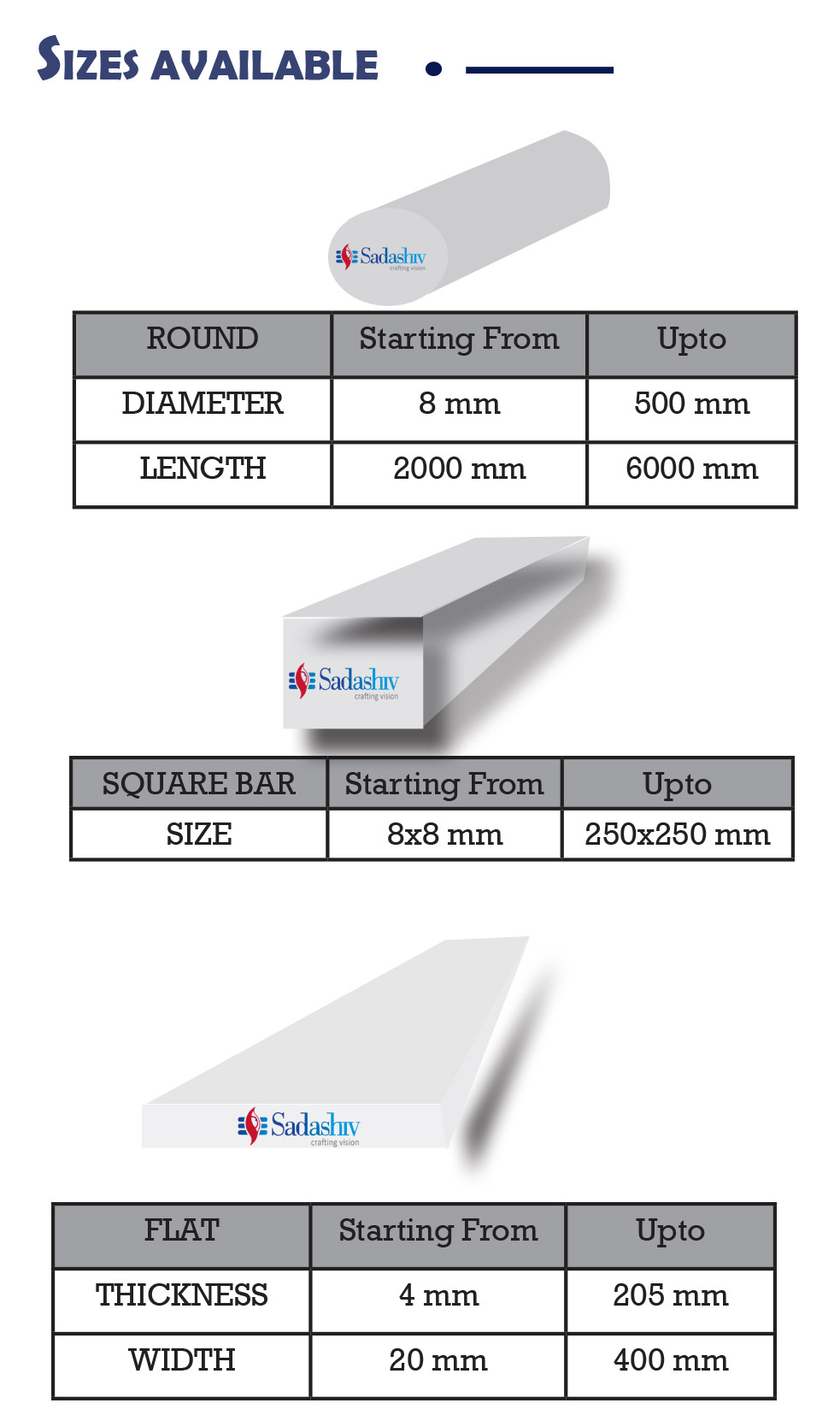
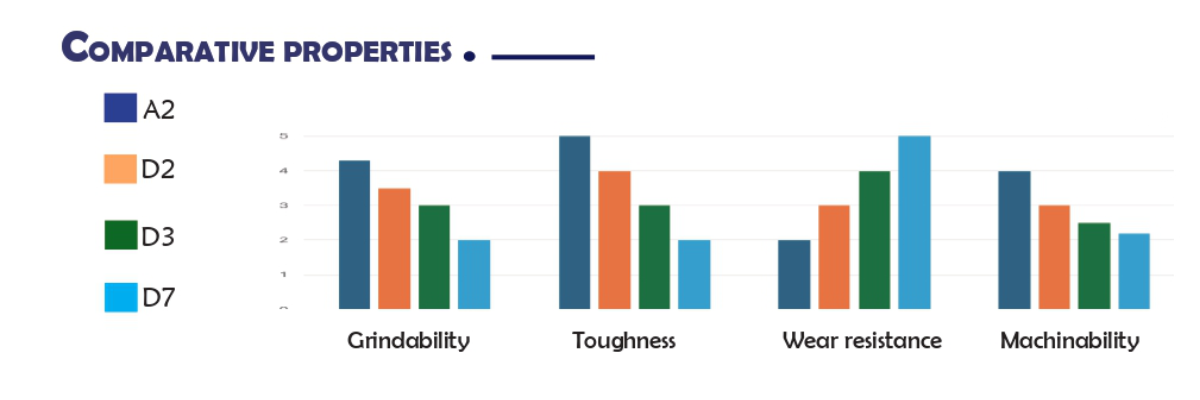