D3 cold-work tool steel is a high-carbon, high-chromium, oil-hardening tool steel that is characterized by a relatively high attainable hardness and numerous, large, chromium-rich alloy carbides in the microstructure. These carbides provide good resistance to wear from sliding contact with other metals and abrasive materials.
» USA: AISI D3
» France: AFNORZ200C12
» Japan: JIS SKD 1
» Germany: 1.2080
CHEMICAL COMPOSITION
C | Cr | SI | Mn | P | S | |
Min | 2.00 | 11.00 | 0.10 | 0.10 | -- | -- |
Typical | 2.15 | 12.25 | 0.35 | 0.35 | -- | -- |
Max | 2.35 | 13.50 | 0.60 | 0.60 | 0.035 | 0.035 |
APPLICATIONS
- » Blanking Dies
- » Forming Dies
- » Press tools
- » Pressure pads
- » Punches
- » Bushes
- » Ejector pins
- » Sheer Blades
FORM SUPPLIED
- » Round bar
- » Flat Bar
- » Plates
- » Square Block
Available surface conditions : hot rolled, ground, peeled, turned, drawn, cold rolled
HEAT TREATMENT
- Stress-releiving: Heat to 650-700ºC. Soak for 2-4 hours then furnace cool.
- Annealing: Heat uniformly to 850-870°C, soak thoroughly, then slow furnace cool at a rate of not more than 25°C per hour to 650°C. The parts may then be air cooled. This should result in a maximum hardness of brinell 248.
- Hardening: D3 tool steel is extremely sensitive to overheating during hardening – do not overheat. Pre heat slowly to 800-850°C, the raise rapidly to
950-970°C and soak until completely equalised. Quench in oil. - Tempering : Heat uniformly and thoroughly to the desired temperature and hold for 25 minutes per cm of thickness. D3 can be double tempered after intermediate cooling to room temperature.
Tool | Hardening | Tempering |
single edge cutting tools | 1220 ºC | 550-570 ºC |
multi edge cutting tools | 1180-1220 ºC | 550-570 ºC |
cold work tools | 1050-1150 ºC | 550-570 ºC |
PROCESSING
D3 can be worked as follows :
- Machining( grinding, turning, milling)
- Polishing
- Hot forming
- Electrical discharge machining
- Welding(special procedure incl. pre-heating & filler
materials of base material composition)
GRINDING
During Grinding, local heating of the surface, which can alter the temper, must be avoided. Grinding wheel manufacturers can provide advise on the choice of grinding wheels
SURFACE TREATMENT
The Steel Grade is a perfect substrate material for PVD coating. If nitriding is requested, a small diffusion zone is recommended but avoid compound and oxidized layers.
DELIVERY HARDNESS
- » Typical soft annealed hardness is 260 HB
- » Cold drawn and cold rolled material is typically 10-40 HB harder
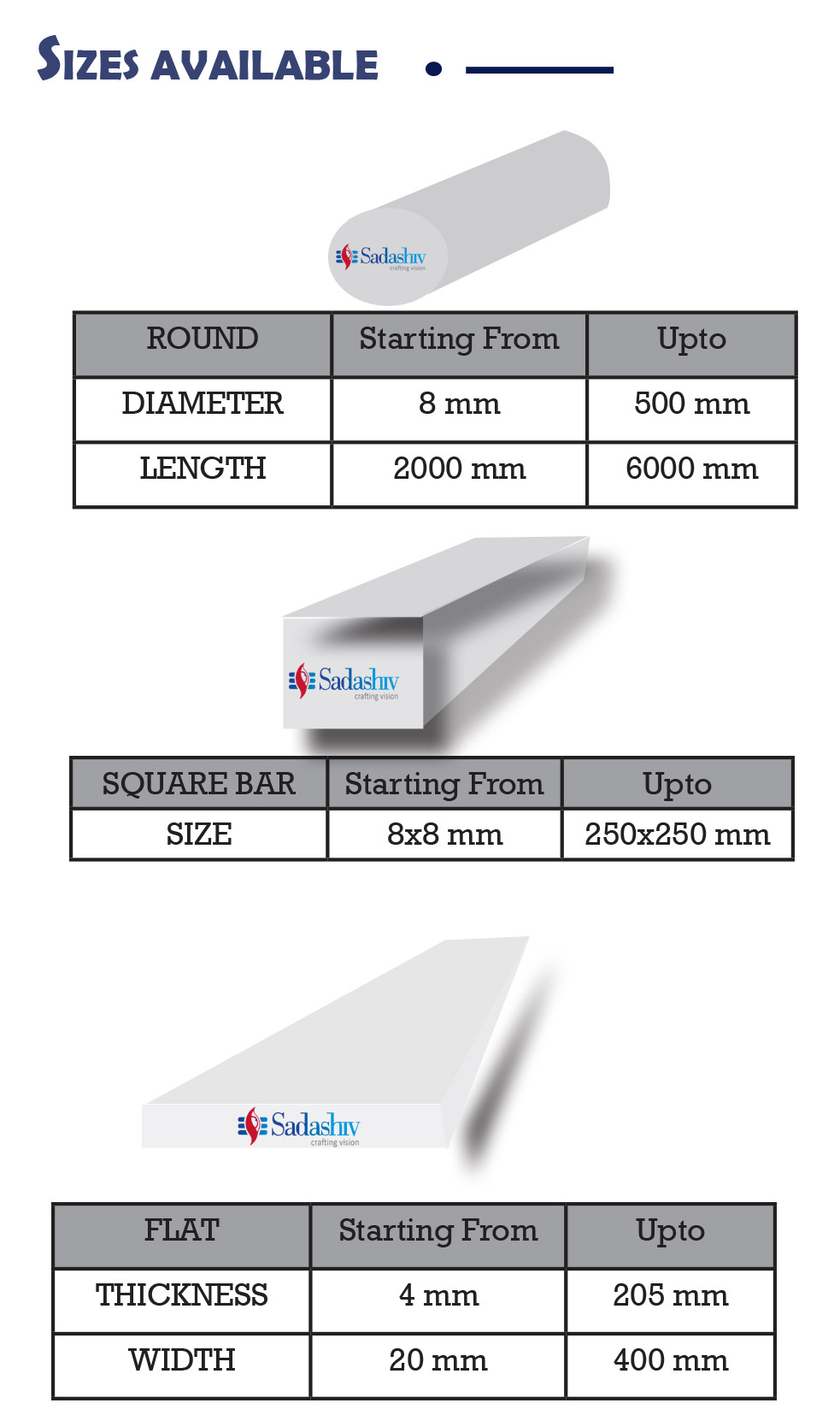
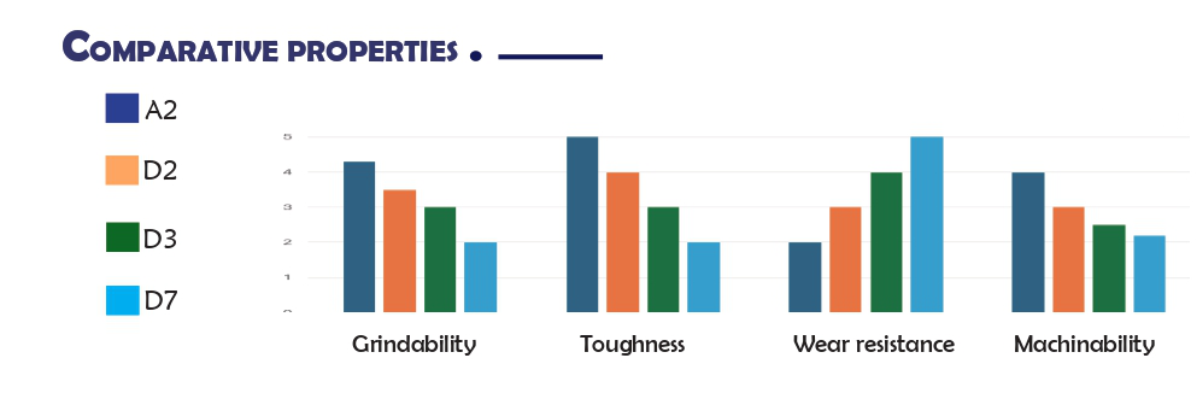