DIN 1.2631 is a medium alloyed cold work steel. It has good thorough hardenability, high wear resistance and very good toughness.
» DIN 1.2631
» X50CrMoW9-1-1
» X50CrMoW9-1-1
CHEMICAL COMPOSITION
C | Cr | SI | Mn | Mo | Ni | W | Cu | P | S | |
Min | 0.45 | 8.00 | 0.80 | 0.40 | 1.10 | 1.10 | -- | -- | -- | |
Typical | 0.50 | 8.50 | 0.90 | 0.50 | 1.20 | 1.20 | -- | -- | ||
Max | 0.55 | 9.00 | 1.00 | 0.60 | 1.30 | 0.25 | 1.30 | 0.25 | 0.035 | 0.035 |
APPLICATIONS
- » Wood working knives
- » Straight and round cutting blades
- » Blades used in paper industry
FORM SUPPLIED
- » Round bar
- » Plates
- » Square Block
- » Flat Bar
Available surface conditions : hot rolled, ground, peeled, turned, drawn, cold rolled
HEAT TREATMENT
- Annealing: Annealing temperature/ 0 C: 750~800; After the annealing, degree of hardness ≤HBS: 230
- Quenching: Hardening temperature/ 0 C:1020~1050, Quenching in oil
- Tempering: Commonly used drawing temperature/ °C: 180~250;
After tempering hardness HRC | 100 °C: 58; After tempering hardness HRC | 200 °C : 57; After tempering hardness HRC | 300 °C: 56 ; After tempering hardness HRC | 400 °C: 55 - Normalizing: at Normalizing temperature, then cool in furnace
Tool | Hardening | Tempering |
single edge cutting tools | 1220 ºC | 560 ºC |
multi edge cutting tools | 1180-1220 ºC | 560 ºC |
cold work tools | 1050-1150 ºC | 560 ºC |
PROCESSING
S1 can be worked as follows :
- Machining( grinding, turning, milling)
- Polishing
- Hot forming
- Electrical discharge machining
- Welding(special procedure incl. pre-heating & filler
materials of base material composition)
GRINDING
During Grinding, local heating of the surface, which can alter the temper, must be avoided. Grinding wheel manufacturers can provide advise on the choice of grinding wheels
SURFACE TREATMENT
The Steel Grade is a perfect substrate material for PVD coating. If nitriding is requested, a small diffusion zone is recommended but avoid compound and oxidized layers.
DELIVERY HARDNESS
- » Typical soft annealed hardness is 230 HB
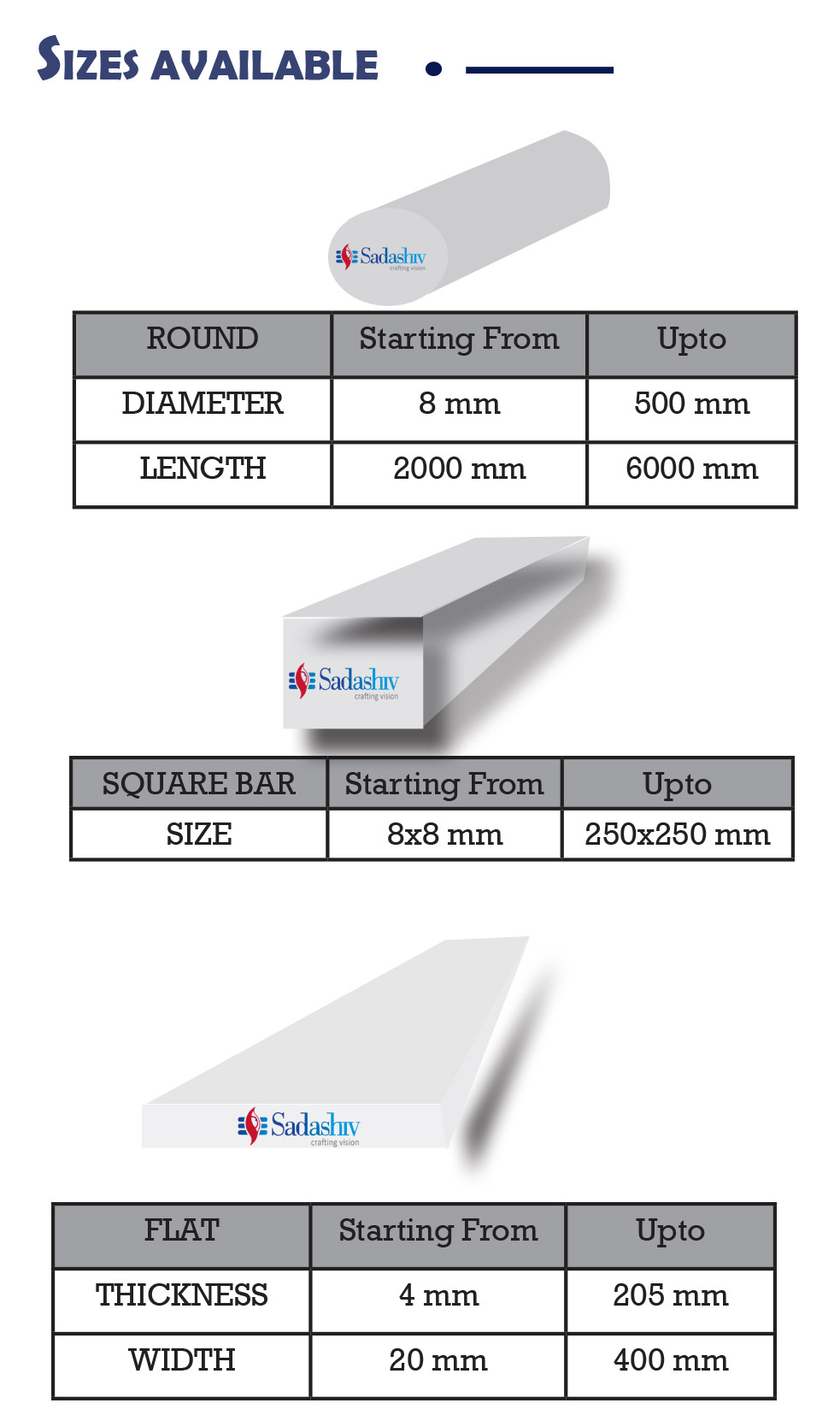