H10 Chromium hot-work steel has excellent resistance to softening at high temperatures. This particular grade is resisitant to thermal fatigue cracking and can be cooled in water for servicing. Typical applications included hot punches, die castings dies, forging dies and extrusion tooling.
» USA: AISI H10
» Japan: JIS SKD7
» UNS T20810
CHEMICAL COMPOSITION
C | Cr | SI | Mn | Mo | V | P | S | |
Min | 0.35 | 3.00 | 0.80 | 0.20 | 2.00 | 0.20 | -- | -- |
Typical | 0.40 | 3.30 | 1.00 | 0.45 | 2.50 | 0.35 | -- | -- |
Max | 0.46 | 3.75 | 1.25 | 0.70 | 3.00 | 0.50 | 0.035 | 0.035 |
APPLICATIONS
- » Hot Punches
- » Die casting dies
- » Forging dies
- » Extrusion Tools
FORM SUPPLIED
- » Flat Bar
- » Round bar
- » Square bar
Available surface conditions : hot rolled, ground, peeled, turned, drawn, cold rolled
HEAT TREATMENT
- Hardening: Heat the steel to 1000–1030°C (1832–1886°F) for 15–30 minutes
- Tempering: Temper the steel at 450–570°C (842–1058°F) for at least 2 hours for smaller pieces and 1 hour per 20mm of thickness for larger pieces.
- Quenching: Cool the steel uniformly and at a sufficient rate to avoid distortion and quench cracking.
- Stress Relieving:Heat the steel to 600–650°C (1112–1202°F) after rough machining.
- Annealing: Heat the steel to 750–800°C (1382–1472°F) for 6–8 hours, then cool it slowly in the furnace to 600°C (1112°F). Finally, cool the steel further in air. .
Tool | Hardening | Tempering |
single edge cutting tools | 1220 ºC | 550-570 ºC |
multi edge cutting tools | 1180-1220 ºC | 550-570 ºC |
cold work tools | 1050-1150 ºC | 550-570 ºC |
PROCESSING
H11 can be worked as follows :
- Machining( grinding, turning, milling)
- Polishing
- Hot forming
- Electrical discharge machining
- Welding(special procedure incl. pre-heating & filler
materials of base material composition)
GRINDING
During Grinding, local heating of the surface, which can alter the temper, must be avoided. Grinding wheel manufacturers can provide advise on the choice of grinding wheels
SURFACE TREATMENT
The Steel Grade is a perfect substrate material for PVD coating. If nitriding is requested, a small diffusion zone is recommended but avoid compound and oxidized layers.
DELIVERY HARDNESS
- » Typical soft annealed hardness is 229 HB
- » Cold drawn and cold rolled material is typically 10-40 HB harder
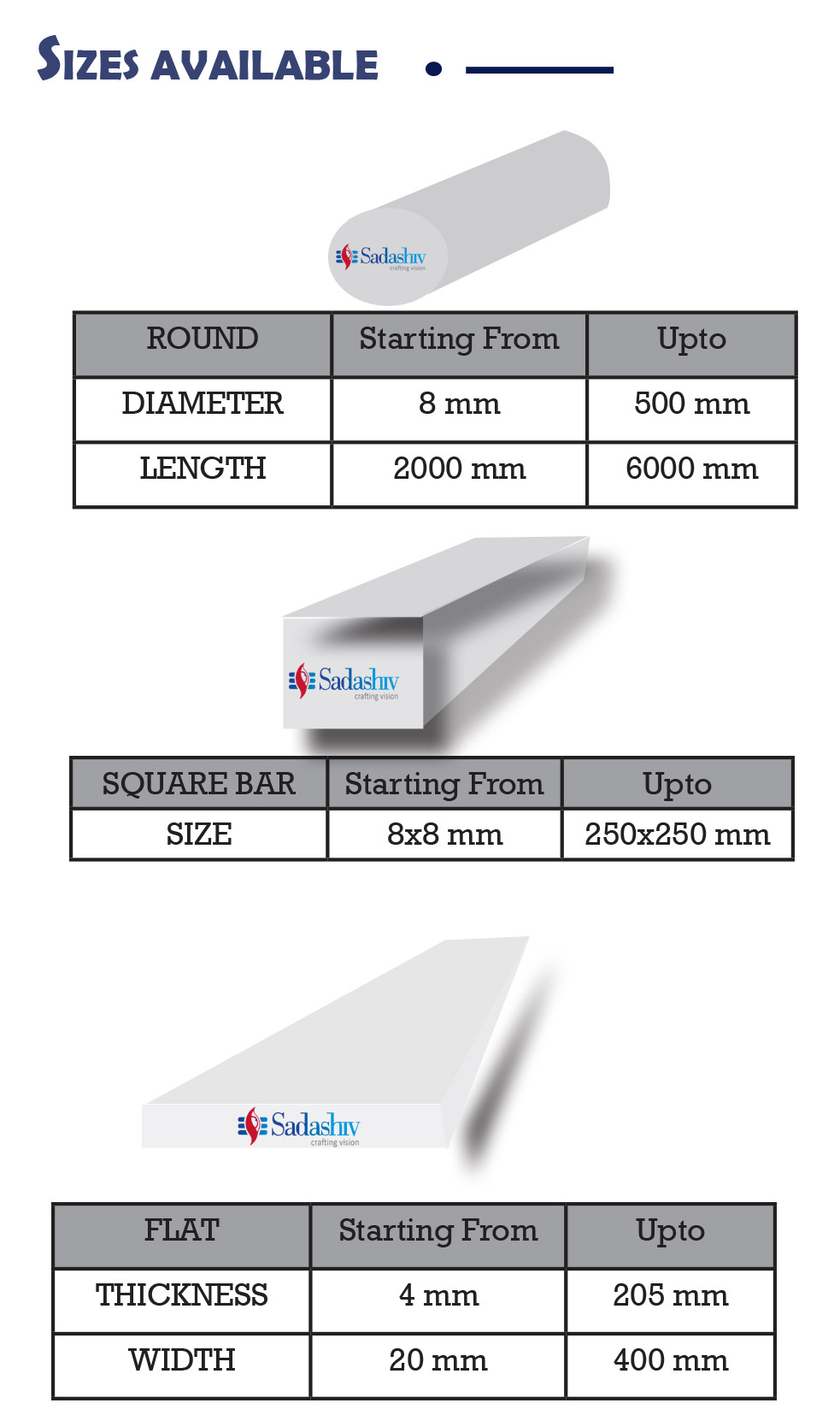
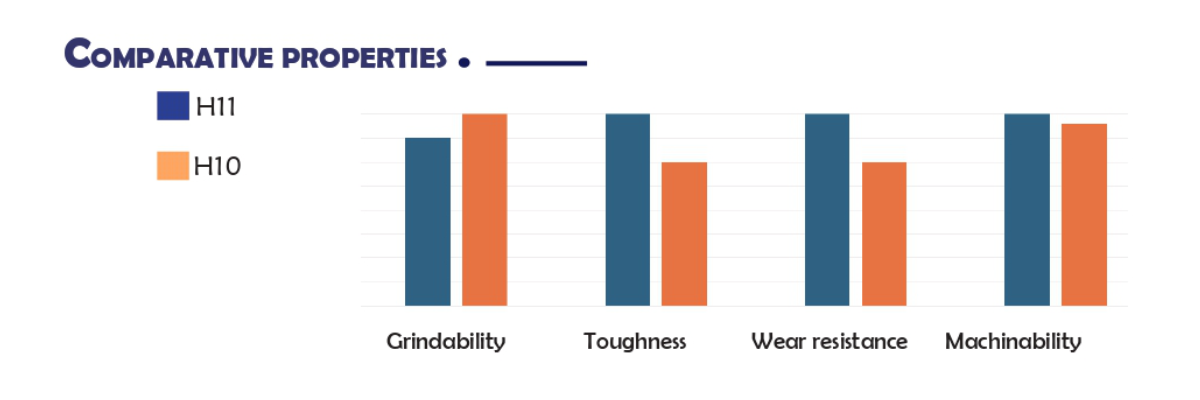