AISI H11, belongs to the category of hot work tool steels. It’s known for its exceptional toughness, resistance to thermal fatigue, and its ability to maintain its properties even at elevated temperatures.
» USA: AISI H11
» Japan: JIS SKD6
» Germany: 1.2343
CHEMICAL COMPOSITION
C | Cr | SI | Mn | Mo | V | P | S | |
Min | 0.35 | 4.75 | 0.80 | 0.20 | 1.10 | 0.30 | -- | -- |
Typical | 0.40 | 5.10 | 1.00 | 0.40 | 1.35 | 0.45 | -- | -- |
Max | 0.45 | 5.50 | 1.25 | 0.60 | 1.60 | 0.60 | 0.035 | 0.035 |
APPLICATIONS
- » Aircraft gear
- » Forming Dies
- » Landing Gear
- » Hot work punches
FORM SUPPLIED
- » Round bar
- » Flat Bar
- » Plates
- » Billet
- » Round bar
- » Square bar
Available surface conditions : hot rolled, ground, peeled, turned, drawn, cold rolled
HEAT TREATMENT
- Hardening: The austenitizing temperature, which should be between 1800° and 1850°F, the steel should be hardened by cooling in still air due to its extremely high hardenability
- Tempering: Quenching H11 steel is tempered to make it more resilient and less brittle. Reheating the steel to a temperature that is lower than its critical temperature—typically between 500°C and 650°C or 932°F and 1202°F—and maintaining it there for a certain amount of time is the process of tempering.
- Forging:is normally done at a temperature between 1000 and 1200 degrees Celsius (1832 and 2192 degrees Fahrenheit). According to the required deformation properties and the manufacturer’s instructions, the precise temperature will vary.
- Stress Relieving:is heated to a particular temperature of 650 °C for two hours as part of the stress-relieving procedure, and it is then gradually cooled.
- Normalizing: Steel should not be normalised due to its air-hardening ability .
Tool | Hardening | Tempering |
single edge cutting tools | 1220 ºC | 550-570 ºC |
multi edge cutting tools | 1180-1220 ºC | 550-570 ºC |
cold work tools | 1050-1150 ºC | 550-570 ºC |
PROCESSING
H11 can be worked as follows :
- Machining( grinding, turning, milling)
- Polishing
- Hot forming
- Electrical discharge machining
- Welding(special procedure incl. pre-heating & filler
materials of base material composition)
GRINDING
During Grinding, local heating of the surface, which can alter the temper, must be avoided. Grinding wheel manufacturers can provide advise on the choice of grinding wheels
SURFACE TREATMENT
The Steel Grade is a perfect substrate material for PVD coating. If nitriding is requested, a small diffusion zone is recommended but avoid compound and oxidized layers.
DELIVERY HARDNESS
- » Typical soft annealed hardness is 229 HB
- » Cold drawn and cold rolled material is typically 10-40 HB harder
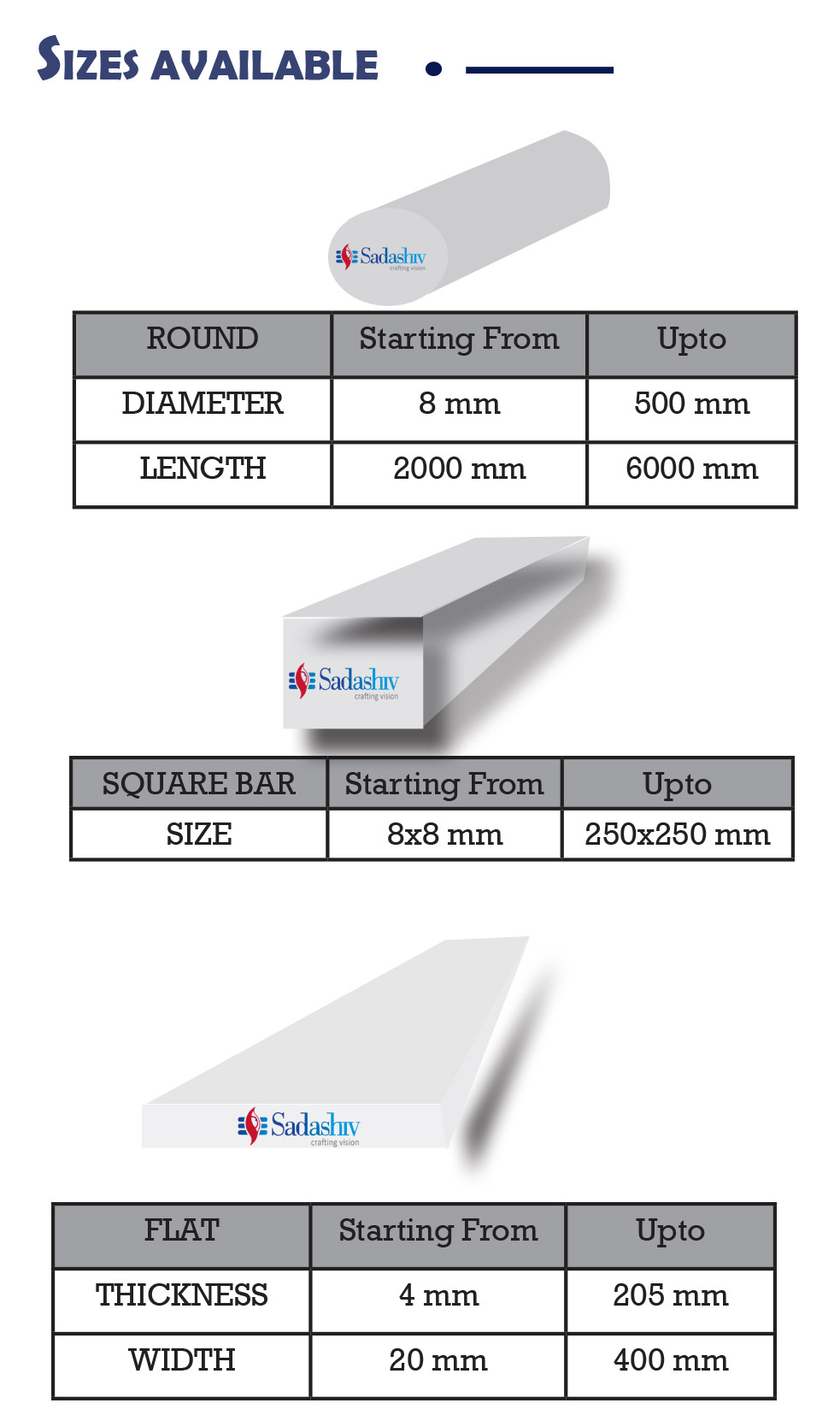
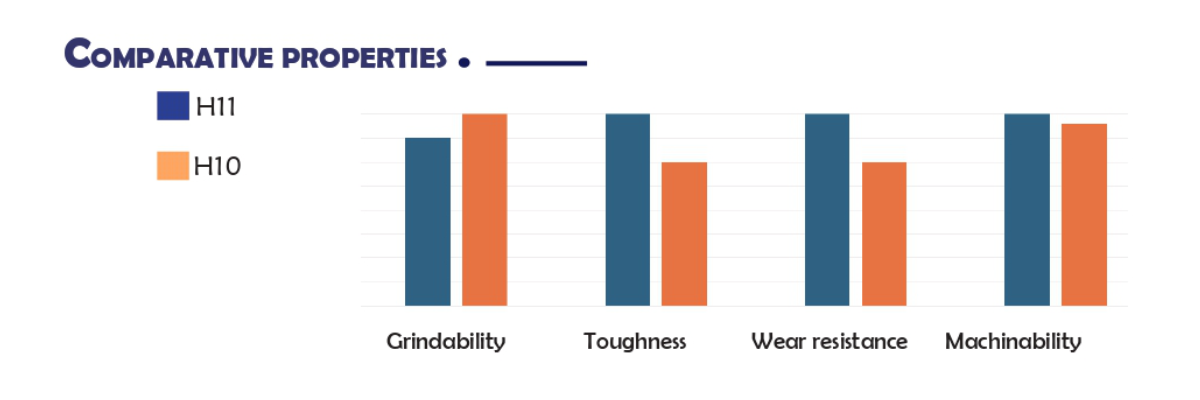