H21 Steel is a hot work tool steel for oil or air hardening to develop high hot quality, support of hardness, and warmth checking resistance. This is mostly utilized as hot work devices, instruments for manufacture of hollows, screws, rivets, nuts and bolts.
» USA: AISI H21
» France: AFNORZ30WCV9
» Japan: JIS SKD5
» UK: BH21
C | Cr | SI | Mn | V | W | P | S | Cu | |
Min | 0.26 | 3.00 | 0.15 | 0.15 | 0.30 | 8.50 | -- | -- | -- |
Typical | 0.30 | 3.35 | 0.30 | 0.25 | 0.45 | 9.25 | |||
Max | 0.36 | 3.75 | 0.50 | 0.40 | 0.60 | 10.00 | 0.035 | 0.035 | 0.25 |
APPLICATIONS
- » Extrusion Tools
- » Forming Dies
- » Press Dies
- » Hot Shear Blades
- » Hot Punch tool
- » Dies for die carbide
- » Immediate Roller for
Cold Rolling
FORM SUPPLIED
- » Round bar
- » Flat Bar
- » Square Bar
- » Plate
- » Hexagonal Bar
- » Sheets
- » Steel Block
Available surface conditions : hot rolled, ground, peeled, turned, drawn, cold rolled
HEAT TREATMENT
- Stress-releiving : Heat to 600°C / 650°C. Hold for 2-4 hours and furnace cool.
- Annealing : Pack preferably in a suitable sealed container with spent carburising mixture or cast iron chippings to prevent excessive scaling or decarburisation. Heat to 850°C / 880°C, holding at temperature for sufficient time to achieve uniformity. Cool at less than 25°C per hour to 650°C followed by air cooling. Correctly annealed the tools or parts should not exceed 248 HB
- Hardening: Before heat treatment, sufficient machining should be carried out to remove surface decarburisation. Hardening should be carried out in
controlled atmosphere furnaces or neutral salt baths. Preheat slowly to 800°C / 850°C then transfer to a bath or furnace at 1120°C / 1170°C allowing sufficient time for uniform heating. Quench into warm oil or salt bath operating at 520°C / 540°C. In the latter case ensure that the tools are allowed to equalise before completing the quench by cooling in air
- Tempering: Tempering should be carried out immediately after proper completion of the
quenching operation. Heat to within the 560°C/ 675°C range soaking for two to three hours according to section. A second tempering cycle of similar duration is strongly recommended and care should be taken to ensure that the tools are allowed to cool to room temperature al least 50°C higher than that which the tools may be expected to achieve in service. The curve given indicates typical hardness values obtained on oil quenching from 1160°C and double tempering - Forging: : Forging of the H21 steels can be performed at 1150°C (2100°F) down to 927°C (1700°F) but not below 899°C (1650°F)
Tool | Hardening | Tempering |
single edge cutting tools | 1220 ºC | 550-570 ºC |
multi edge cutting tools | 1180-1220 ºC | 550-570 ºC |
cold work tools | 1050-1150 ºC | 550-570 ºC |
PROCESSING
H21 can be worked as follows :
- Machining( grinding,turning,milling)
- Polishing
- Hot forming
- Electrical discharge machining
- Welding(special procedure incl. pre-heating & filler
materials of base material composition)
GRINDING
During Grinding, local heating of the surface, which can alter the temper, must be avoided. Grinding wheel manufacturers can provide advise on the choice of grinding wheels
SURFACE TREATMENT
The Steel Grade is a perfect substrate material for PVD coating. If nitriding is requested, a small diffusion zone is recommended but avoid compound and oxidized layers.
DELIVERY HARDNESS
- » Typical soft annealed hardness is 250 HB
- » Cold drawn and cold rolled material is typically 10-40 HB harder
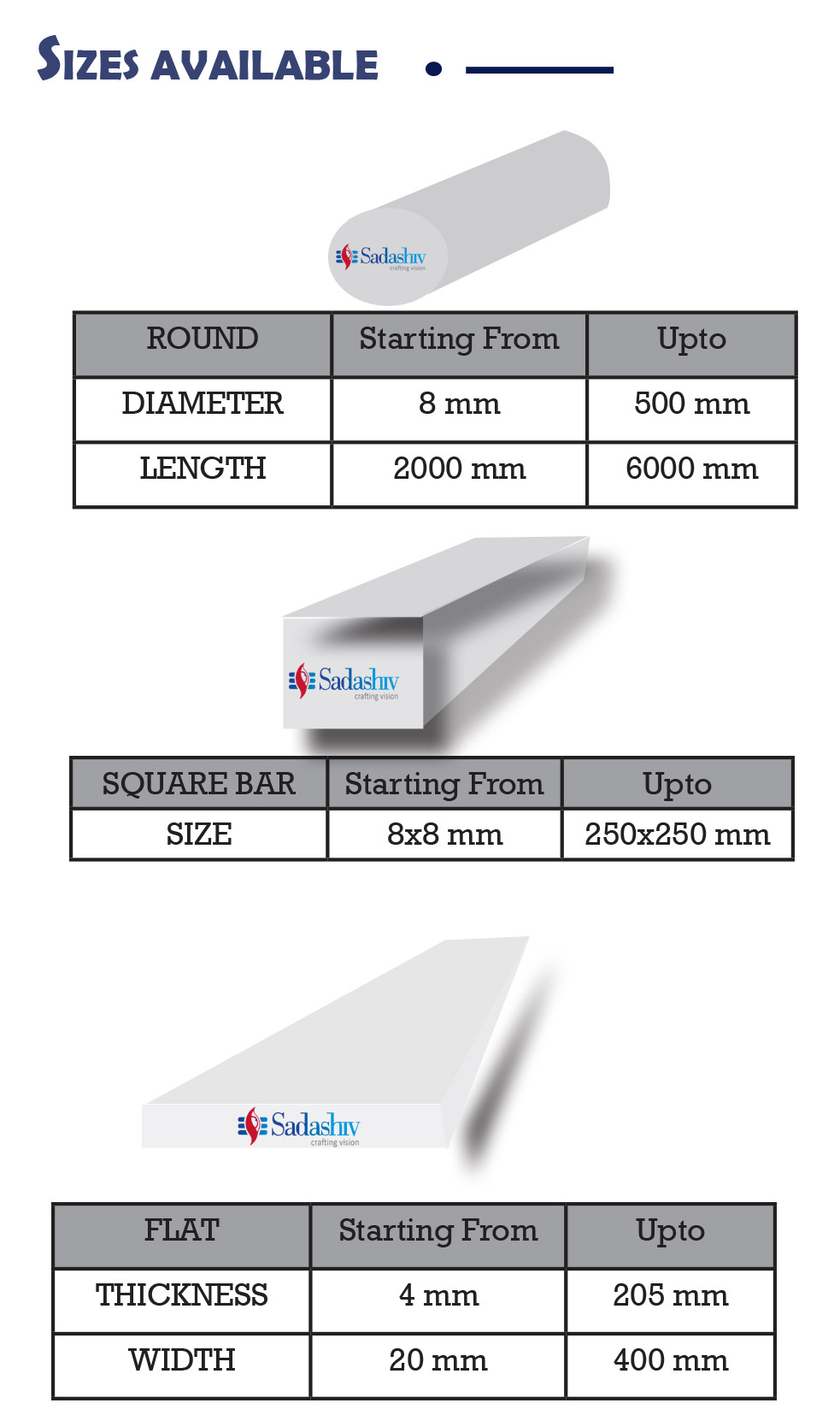
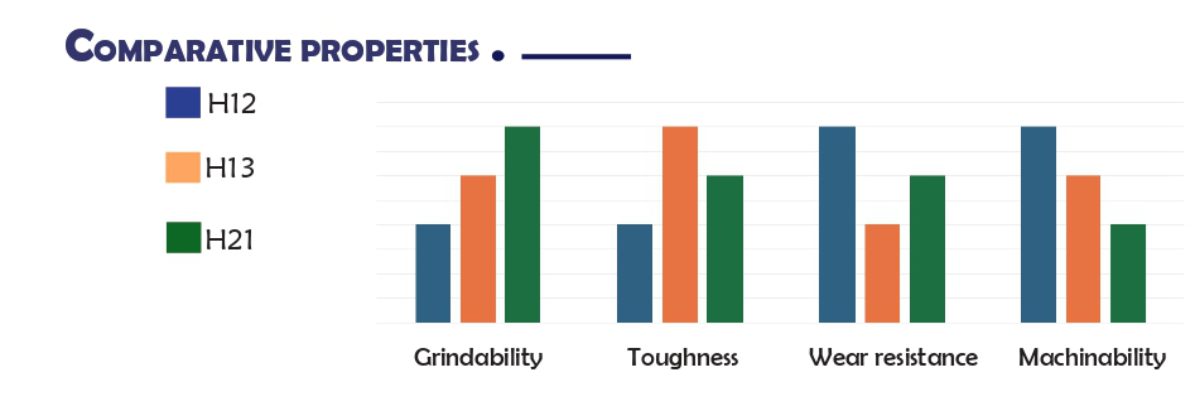