M-50 steel is a premium-melted alloy refined using vacuum-induction melting (VIM) and vacuum-arc remelting (VAR) exhibiting excellent resistance to multi-axial stresses and softening at high service temperatures, as well as good resistance to oxidation.
» USA: AISI M50
» Europe: HS 0-4-1
» Germany: 1.3325
» UK: BM50
» France: AFNORY80DCV.42.16
CHEMICAL COMPOSITION:-
C | Cr | SI | Mn | Mo | V | P | S | |
Min | 0.78 | 3.75 | 0.20 | 0.15 | 3.90 | 0.80 | -- | -- |
Typical | 0.83 | 4.10 | 0.40 | 0.30 | 4.30 | 1.00 | -- | -- |
Max | 0.88 | 4.50 | 0.60 | 0.45 | 4.75 | 1.25 | 0.035 | 0.035 |
APPLICATIONS
- » Aircraft Engine bearings
- » Gas Turbines
- » Helicopter rotor
bearings
FORM SUPPLIED
- » Billet
- » Round Bar
- » Flat Bar
- » Forging
- » Ring
- » Tubing
Available surface conditions : drawn, ground, rolled, hot rolled, cold rolled, peeled, turned.
HEAT TREATMENT
Annealing : Annealing is carried out at 1600° F (870 °C), followed by cooling slowly to room temperature. Please note that. Steel M-50 is susceptible to decarburization, which is not a wanted property given its use in tools and bearings. To mitigate decarburization, use inert or reduced-pressure atmosphere during the annealing process.
Hardening: Hardening should be carried out after annealing. To properly harden Steel M-50, preheat the part to 1500° F(815° C) until the whole component is
heated correctly. After preheating, increase the temperature to 2000° F(1090° C) for superheating. As with the preheating step, ensure that the whole part
is heated equally before proceeding to immediate quenching in salt bath furnace or controlled atmosphere furnace. After the part was cooled using the
quenching method, cool the piece to -100° F (-73° C) for 1 hour.
Tempering: should be done immediately after quenching, with double tempering at 1025° F (550° C)recommended for achieving the best properties.
Tool | Hardening | Tempering |
multi edge cutting tools | 1100-1120 ºC | 550-570 ºC |
cold work tools | 1080-1120 ºC | 550-570 ºC |
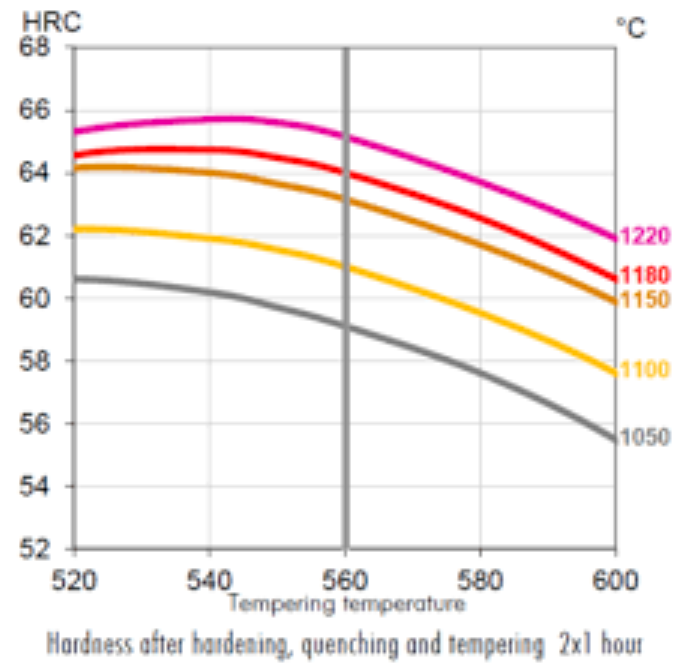
PROCESSING
M50 can be worked as follows :
- Machining( grinding,turning,milling)
- Polishing
- Hot forming
- Electrical discharge machining
- Welding(special procedure incl. pre-heating & filler
materials of base material composition)
GRINDING
During Grinding, local heating of the surface, which can alter the temper, must be avoided. Grinding wheel manufacturers can provide advise on the choice of grinding wheels.
SURFACE TREATMENT
The Steel Grade is a perfect substrate material for PVD coating. If nitriding is requested, a small diffusion zone is recommended but avoid compound and oxidized layers.
DELIVERY HARDNESS
- » Typical soft annealed hardness is 225 HB
- » Cold drawn and cold rolled material is typically 10-40 HB harder
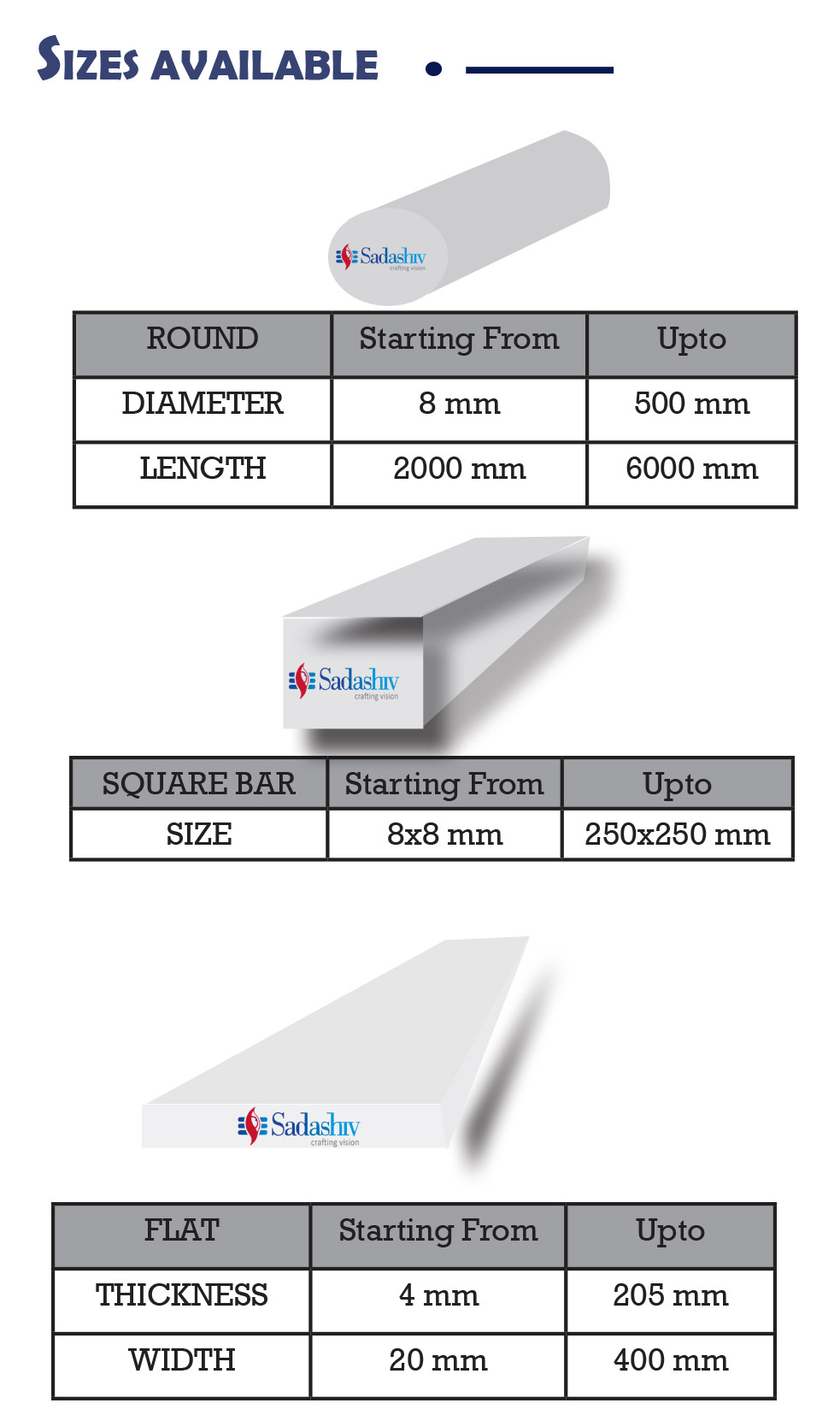
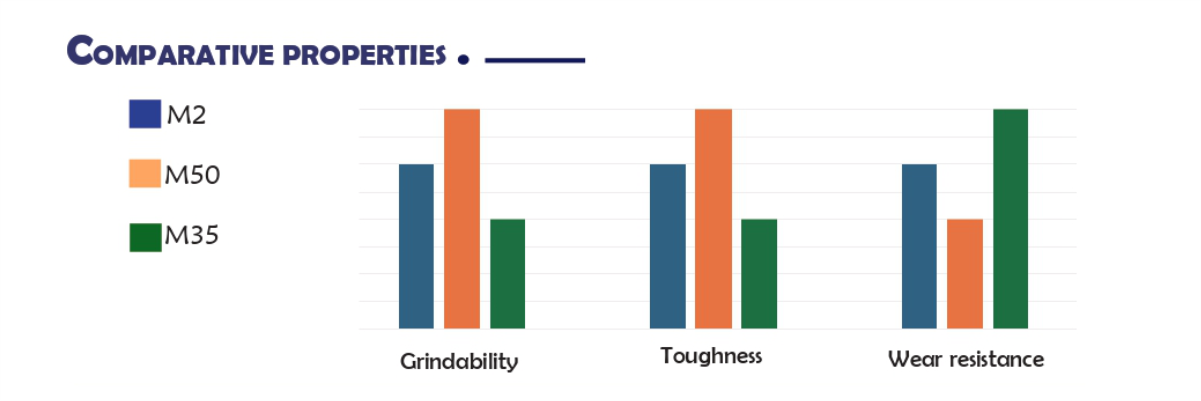