M35 high speed tool steel : is suitable for heat treatment up to 66 HRC, and also offers excellent cutting performance and offers excellent cutting performance. This kind of steel is suitable for conditions involving thermal stresses and discontinuous cutting.
» Germany: 1.3243
» Sweden: SS 2723
» Japan: JIS SKH55
» France: AFNOR Z90WDKCV6.5.5.4.2
» USA: AISI M35
» Europe: HS 6-5-2-5
C | Cr | SI | Mn | Mo | W | V | Co | P | S | |
Min | 0.86 | 3.75 | 0.20 | 0.20 | 4.50 | 5.50 | 1.70 | 4.50 | -- | -- |
Typical | 0.9 | 4.00 | 0.30 | 0.30 | 5.00 | 6.00 | 1.90 | 4.70 | ||
Max | 0.94 | 4.50 | 0.40 | 0.40 | 5.50 | 6.70 | 2.10 | 5.00 | 0.035 | 0.035 |
APPLICATIONS
- » End Mills
- » Cutters
- » Hobs
- » Milling cutters
- » Broaches
- » Saws
- » Cold work
FORM SUPPLIED
- » Drawn wire
- » Square bars
- » Discs
- » Sheets
- » Strips
- » Round bars
- » Flat bars
- » Wire rod
Available surface conditions : drawn, ground, rolled, hot rolled, cold rolled, peeled, turned.
HEAT TREATMENT
- Stress-releiving at 600ºC to 700ºC for approximately 2hours, slow cooling down to 500 ºC.
- Hardening in a protective atmosphere with pre-heating in 2 steps at 450-500 ºC and 850-900 ºC and austenitising at a
temperature suitable for chosen working hardness. 2 tempers at 560 ºC are recommended with atleast 1 hour holding time, each time. - Hardening in a protective atmosphere at 850-900 ºC for 3 hours, followed by slow cooling 10ºC per hour down to 700ºC, then air cooling.
Tool | Hardening | Tempering |
single edge cutting tools | 1220 ºC | 560 ºC |
multi edge cutting tools | 1180-1220 ºC | 550-570 ºC |
cold work tools | 1050-1150 ºC | 550-570 ºC |
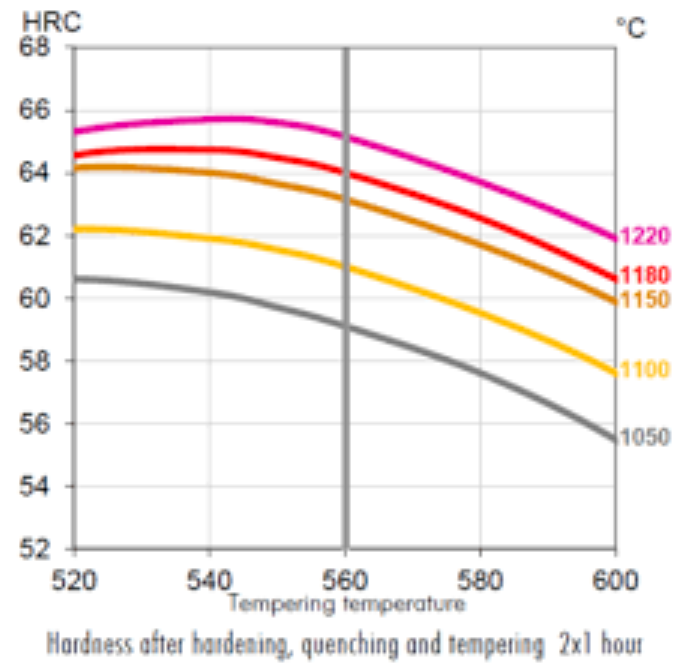
PROCESSING
M35 can be worked as follows :
- Machining( grinding,turning,milling)
- Polishing
- Hot forming
- Electrical discharge machining
- Welding(special procedure incl. pre-heating & filler
materials of base material composition)
GRINDING
During Grinding, local heating of the surface, which can alter the temper, must be avoided. Grinding wheel manufacturers can provide advise on the choice of grinding wheels.
SURFACE TREATMENT
The Steel Grade is a perfect substrate material for PVD coating. If nitriding is requested, a small diffusion zone is recommended but avoid compound and oxidized layers.
DELIVERY HARDNESS
- » Typical soft annealed hardness is 250 HB
- » Cold drawn and cold rolled material is typically 10-40 HB harder
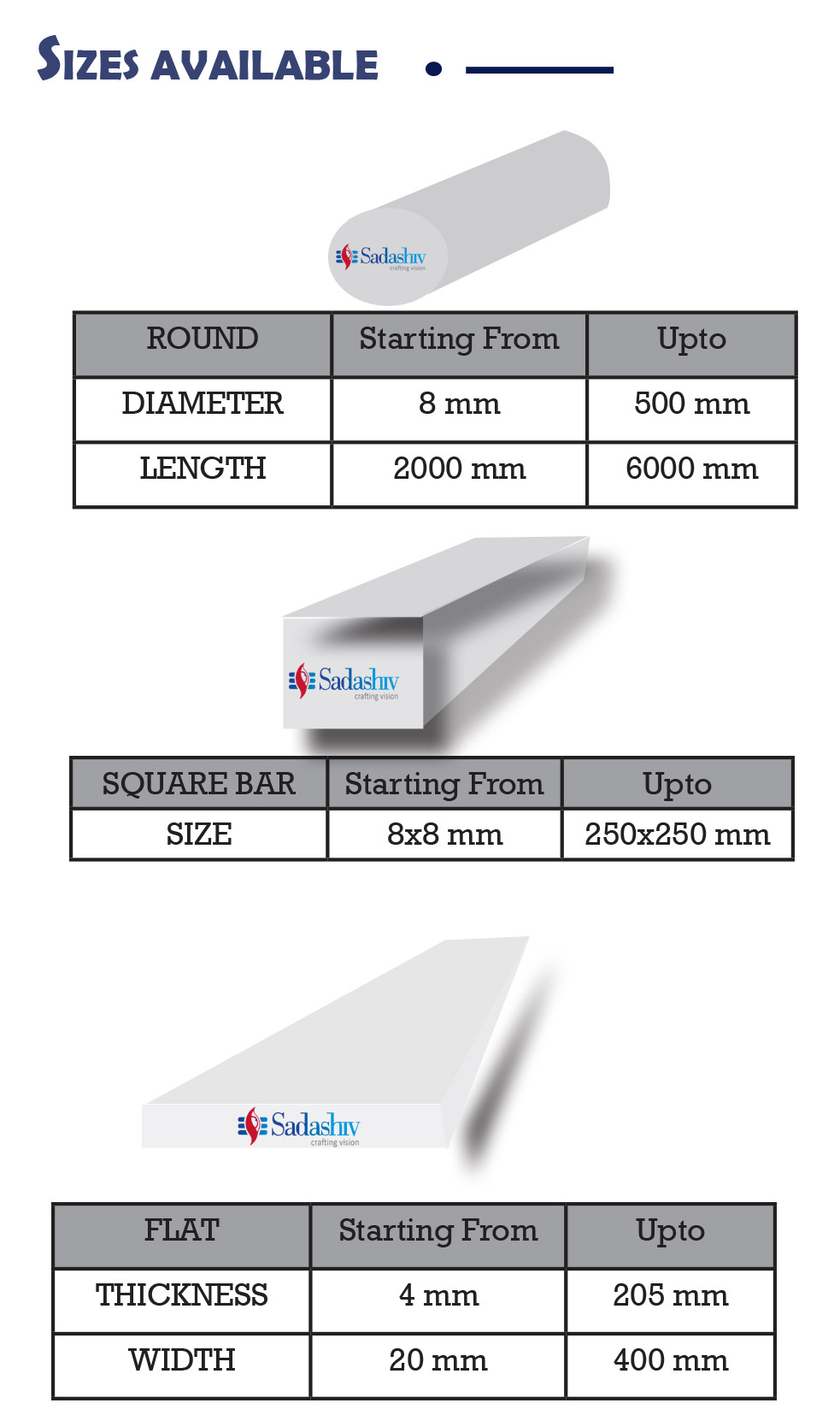
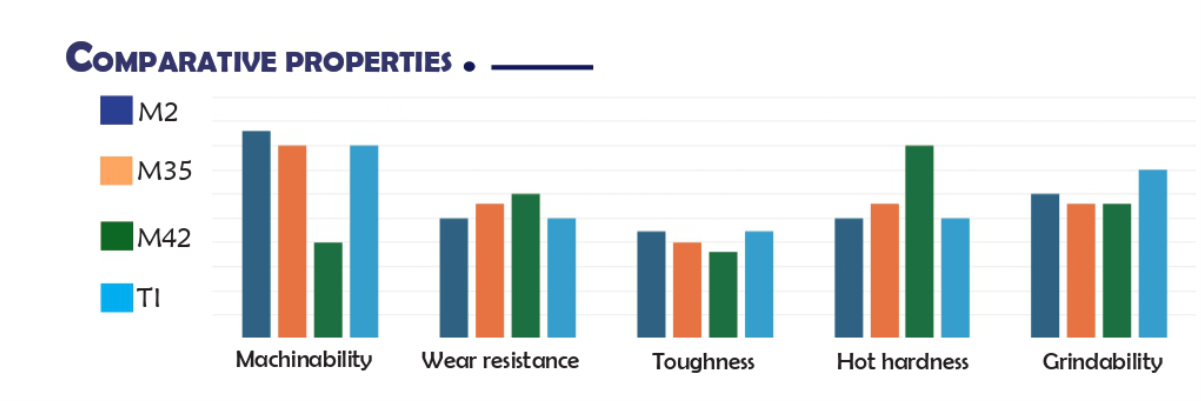