O1 Tool Steel is a low alloy cold work tool steel that must be oil-quenched in heat treatment. Tools and dies made from O1 tool steel flat or rounds will have good wearing and abrasive qualities since the tungsten and higher chromium content gives improved wear resistance.
» USA: AISI O1
» Japan: JIS SK3
» Germany: 1.2510
C | Cr | SI | Mn | V | W | P | S | |
Min | 0.85 | 0.40 | 0.10 | 1.00 | -- | 0.40 | -- | -- |
Typical | 0.90 | 0.55 | 0.30 | 1.20 | 0.50 | -- | -- | |
Max | 1.00 | 0.70 | 0.50 | 1.40 | 0.30 | 0.60 | 0.035 | 0.035 |
APPLICATIONS
- » Blanking Dies
- » Forming Dies
- » Trim Dies
- » Stamps
- » Machine parts
- » Cutters
- » Jigs
- » Bending Dies
FORM SUPPLIED
- » Decarb free rounds
- » Flat Bar
- » Square
Available surface conditions : hot rolled, ground, peeled, turned, drawn, cold rolled
HEAT TREATMENT
- Forging: Heating for forging of oil tool steel O1 must be done slowly and uniformly. Forging of alloy O1 steels can be performed at 980-1000°C, and reheat as often as necessary. But not forge below 800°C. After forging AISI O1 tool steel, cool slowly in lime, mica, dry ashes or furnace. ASTM O-1 tool steels should always be annealed after forging
- Annealing: must be performed after hot working and before re-hardening. Heat at a rate not exceeding 222°C per hour to 802-816°C, and hold at temperature for 1 hour per inch (25.4mm) of maximum thickness; 2 hours minimum. Then cool slowly with the furnace at a rate not exceeding 28°C per hour to 538°C. Continue cooling to ambient temperature in the furnace or in air. The resultant hardness should be a maximum of 212 HBW.
- Hardening: Warm slightly before charging into the preheat furnace, which should be operating at about 1100°-1200°F. Hardening: Heat to 1475
to 1500° F. Soak at heat for 30 minutes per inch of thickness. - Quench: Quench O1 steel in warm oil and allow to cool in the oil until a temperature of 125°-150°F has been reached, or to where the part can be held
in the bare hand, and temper immediately. - Temper: Normally oil hardening steels need to be single tempered only. However, double tempering may sometimes be preferred. Soak at heat for 2 hours per inch of thickness for each temper. Air cool to room temperature between tempers. The normal tempering range for this grade is 300 to 450° F.
Tool | Hardening | Tempering |
single edge cutting tools | 1220 ºC | 550-570 ºC |
multi edge cutting tools | 1180-1220 ºC | 550-570 ºC |
cold work tools | 1050-1150 ºC | 550-570 ºC |
PROCESSING
O1 can be worked as follows :
- Machining( grinding,turning,milling)
- Polishing
- Hot forming
- Electrical discharge machining
- Welding(special procedure incl. pre-heating & filler
materials of base material composition)
GRINDING
During Grinding, local heating of the surface, which can alter the temper, must be avoided. Grinding wheel manufacturers can provide advise on the choice of grinding wheels
SURFACE TREATMENT
The Steel Grade is a perfect substrate material for PVD coating. If nitriding is requested, a small diffusion zone is recommended but avoid compound and oxidized layers.
DELIVERY HARDNESS
- » Typical soft annealed hardness is 229 HB
- » Cold drawn and cold rolled material is typically 10-40 HB harder
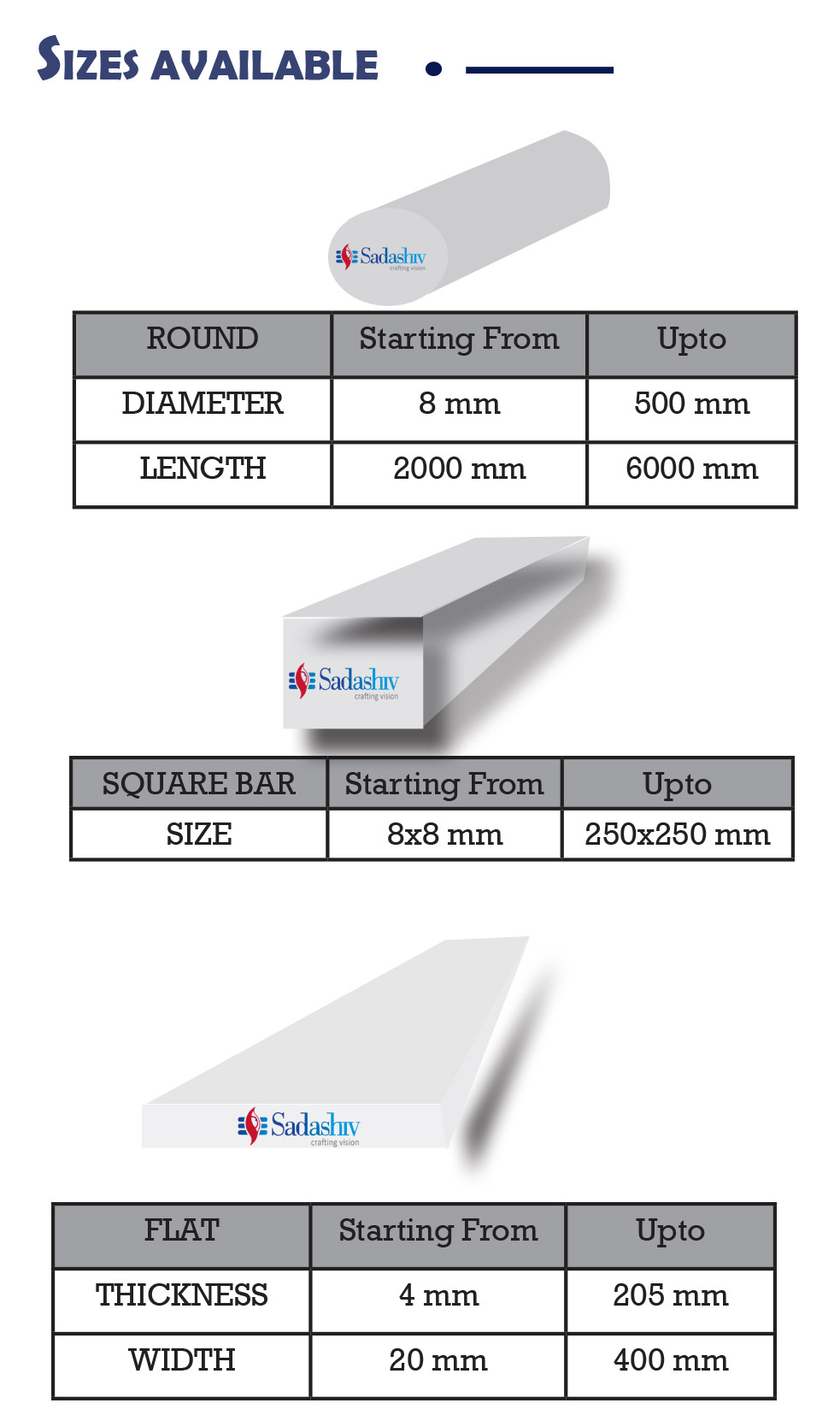
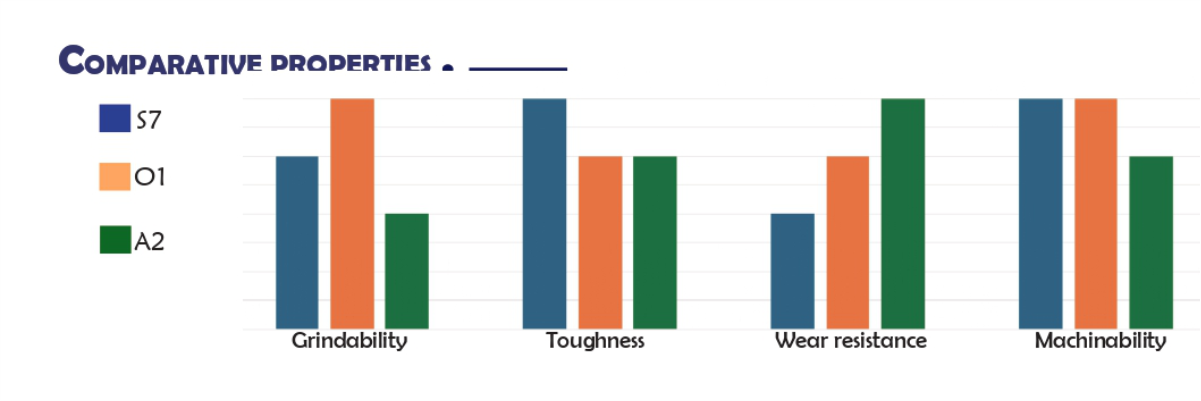