S1 toolsteel is a shock resisting tool steel with very good toughness, is dimensionally stable, and impact resistant, with high hardening capacity. S1 is a shock-resistant, oil-hardening steel with good toughness, dimensional stability, and high hardening capacity.
» USA: AISI S1
» France: AFNOR 55 WC20
» Germany: 1.2550
» China: UNI 58 WCr 9 KU
CHEMICAL COMPOSITION
C | Cr | SI | Mn | Mo | V | W | Cu | P | S | |
Min | 0.40 | 1.00 | 0.15 | 0.20 | -- | 0.15 | 1.50 | -- | -- | -- |
Typical | 0.45 | 1.40 | 0.17 | 0.25 | 0.22 | 2.25 | -- | -- | ||
Max | 0.55 | 1.80 | 1.20 | 0.40 | 0.50 | 0.30 | 3.00 | 0.25 | 0.035 | 0.035 |
APPLICATIONS
- » Cold shear knives
- » Projector pins
- » Coining tools
- » Heavy duty Punches
- » Pneumatic hammers and
chisels
FORM SUPPLIED
- » Round bar
- » Hexagonal bars
- » Plates
- » Square Block
- » Flat Bar
Available surface conditions : hot rolled, ground, peeled, turned, drawn, cold rolled
HEAT TREATMENT
- Forging: S1 tool steels are uniformly preheated at 1000°C (1832°F). These steels are then forged at temperatures ranging from 800 to 1000°C (1472 to 1832°F). This process is followed by cooling in a furnace to avoid stress.
- Annealing: is carried out in S1 tool steels by uniformly heating the steels to 770°C (1418°F)followed
by equalization. These steels are then cooled in the furnace. - Stress Relieving: S1 tools steels are heated up to 700°C (1292°F) before hardening, equalized, and then slowly cooled in order to remove stresses during heavy machining operations.
- Hardening: S1 tools steels are preheated to 650°C (1202°F) and soaked. They are then continuously heated to the nal temperature that ranges from 900 to 950°C (1652 to 1742°F). Finally, the steels are quenched in oil.
- Martempering: performed in the case of S1 tool steels as an alternative procedure for hardening. This is carried out in a salt bath equipment.
- Tempering: S1 tool steels are tempered by uniformly heating the steels at the preferred tempering temperature followed by holding for an hour.
Tool | Hardening | Tempering |
single edge cutting tools | 1220 ºC | 550-570 ºC |
multi edge cutting tools | 1180-1220 ºC | 550-570 ºC |
cold work tools | 1050-1150 ºC | 550-570 ºC |
PROCESSING
S1 can be worked as follows :
- Machining( grinding, turning, milling)
- Polishing
- Hot forming
- Electrical discharge machining
- Welding(special procedure incl. pre-heating & filler
materials of base material composition)
GRINDING
During Grinding, local heating of the surface, which can alter the temper, must be avoided. Grinding wheel manufacturers can provide advise on the choice of grinding wheels
SURFACE TREATMENT
The Steel Grade is a perfect substrate material for PVD coating. If nitriding is requested, a small diffusion zone is recommended but avoid compound and oxidized layers.
DELIVERY HARDNESS
- » Typical soft annealed hardness is 229 HB
- » Cold drawn and cold rolled material is typically 10-40 HB harder
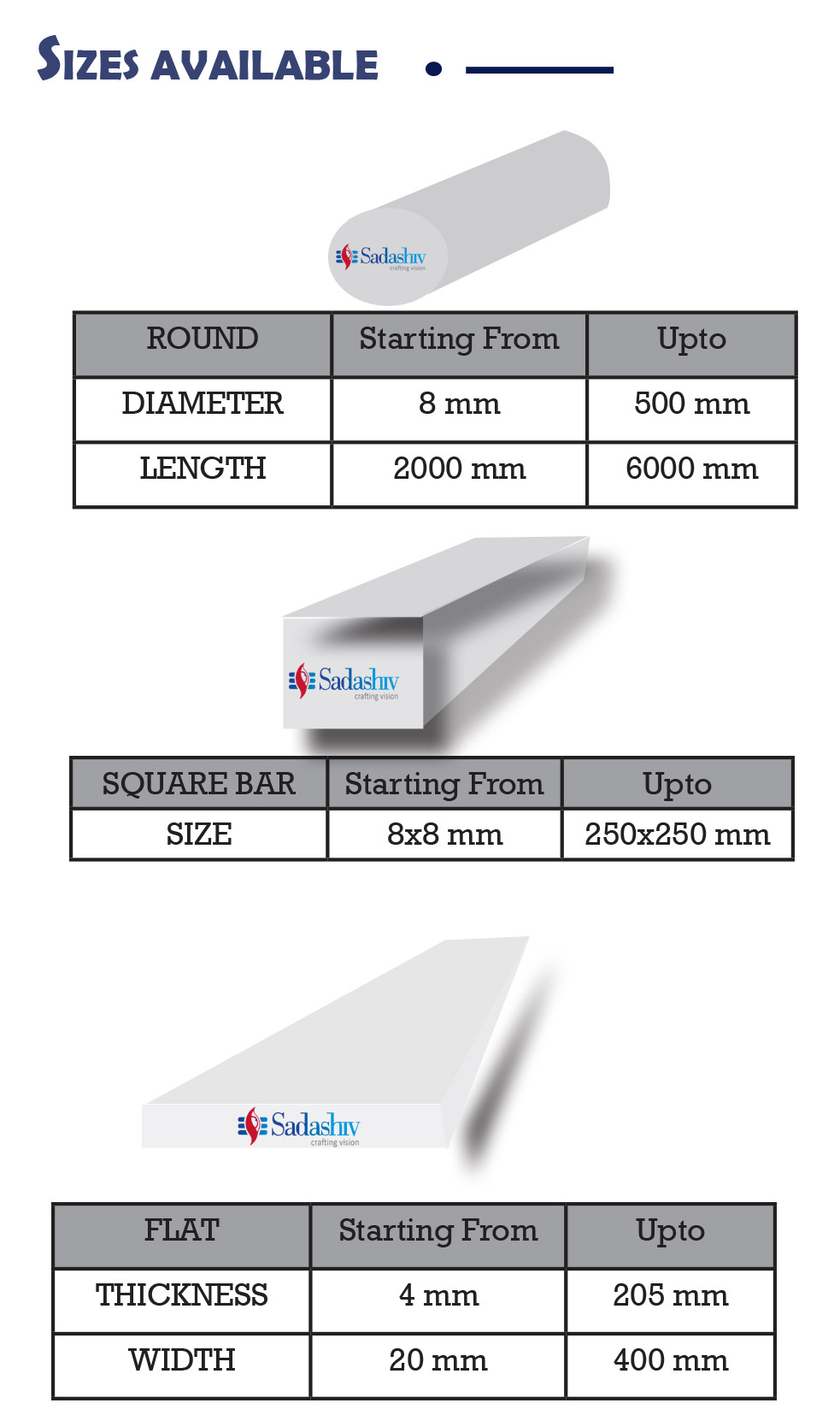
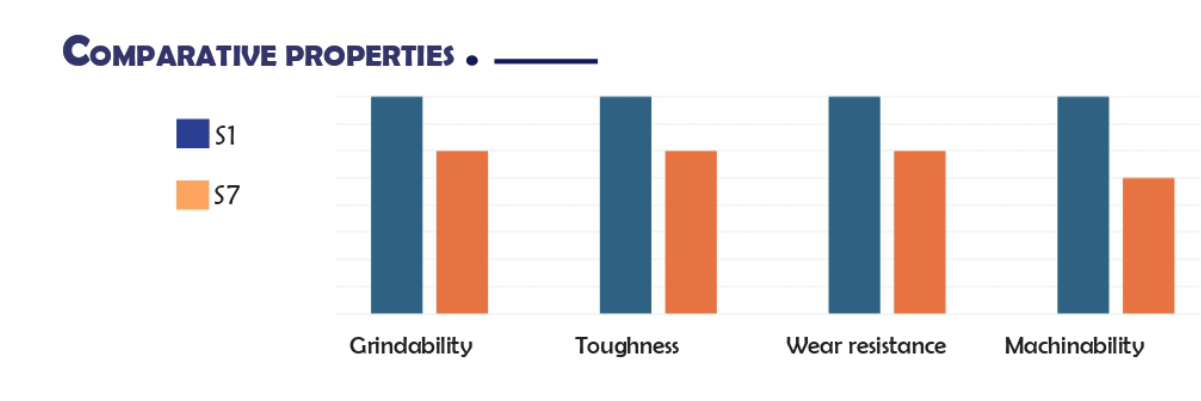