S7 tool steel has exceptional impact properties plus the highest hardenability of shock resisting grades of tool steel. It also possesses good softening resistance at high temperatures which gives it hot work capabilities. Because of its unusual combination of properties,S7 is suitable for a wide range of tool and die applications. It is used for hot and cold shock applications, medium hot-work dies and medium-run cold work tools and dies.
» USA: AISI S7
» Germany: 1.2357
» Europe: 50CrMoV13-15
CHEMICAL COMPOSITION
C | Cr | SI | Mn | Mo | V | P | S | |
Min | 0.40 | 3.00 | 0.20 | 0.20 | 1.30 | 0.15 | -- | -- |
Typical | 0.48 | 3.25 | 0.60 | 0.55 | 0.25 | -- | -- | |
Max | 0.55 | 3.50 | 1.00 | 0.90 | 1.80 | 0.35 | 0.035 | 0.035 |
APPLICATIONS
- » Shear blades
- » Bending Dies
- » Mandrels
- » Collets
- » Leaf springs
- » Pipe cutters
- » Punches
- » Plastic moulds
FORM SUPPLIED
- » Round bar
- » Drill round
- » Plates
- » Square Block
- » Rectangular bars
Available surface conditions : hot rolled, ground, peeled, turned, drawn, cold rolled
HEAT TREATMENT
- Annealing : Anneal in a protective atmosphere. Heat rapidly to 1500 to 1550°F and hold at that temperature for one and one-half hours for each inch of
greatest thickness. To obtain best machining properties, cool slowly to 1000°F, and then air-cool. This annealing procedure should produce a hardness of
Brinell 197 max. - Stress Relief : S7 steel Material: When desirable to relieve the strains of machining, heat slowly to 1050°-1250°F, allow to equalize, then cool in air.
- Hardening: Preheat: Warm steel S7 slightly before charging into the preheat furnace 1200°-1300°F, prior to hardening.
- Harden: 1750°F. Quench S7 tool steel in air if cross section is 2-1/2” or smaller; sections 2-1/2” to 6” should be oil quenched to black (1000°F) followed by air cooling to 150°F. Larger cross sections of S7 steel should be oil quenched to 150°F
- Quench: Quench in still air or dry air blast.
- Temper: Tool steel S7 is normally tempered one hour per inch of section thickness to desired heating rate of 2 hours per inch. Cool in air to room temperature between the two tempers. The tempering temperature varies according to the intended use.
- Suggested: For cold-working and similar applications, the recommend400°-500°F. Hot working applications: apply a tempering temperature of 900°-
1000°F. Never temper at less than 400°F.
Tool | Hardening | Tempering |
single edge cutting tools | 1220 ºC | 550-570 ºC |
multi edge cutting tools | 1180-1220 ºC | 550-570 ºC |
cold work tools | 1050-1150 ºC | 550-570 ºC |
PROCESSING
S7 can be worked as follows :
- Machining( grinding, turning, milling)
- Polishing
- Hot forming
- Electrical discharge machining
- Welding(special procedure incl. pre-heating & filler
materials of base material composition)
GRINDING
During Grinding, local heating of the surface, which can alter the temper, must be avoided. Grinding wheel manufacturers can provide advise on the choice of grinding wheels
SURFACE TREATMENT
The Steel Grade is a perfect substrate material for PVD coating. If nitriding is requested, a small diffusion zone is recommended but avoid compound and oxidized layers.
DELIVERY HARDNESS
- » Typical soft annealed hardness is 220 HB
- » Cold drawn and cold rolled material is typically 10-40 HB harder
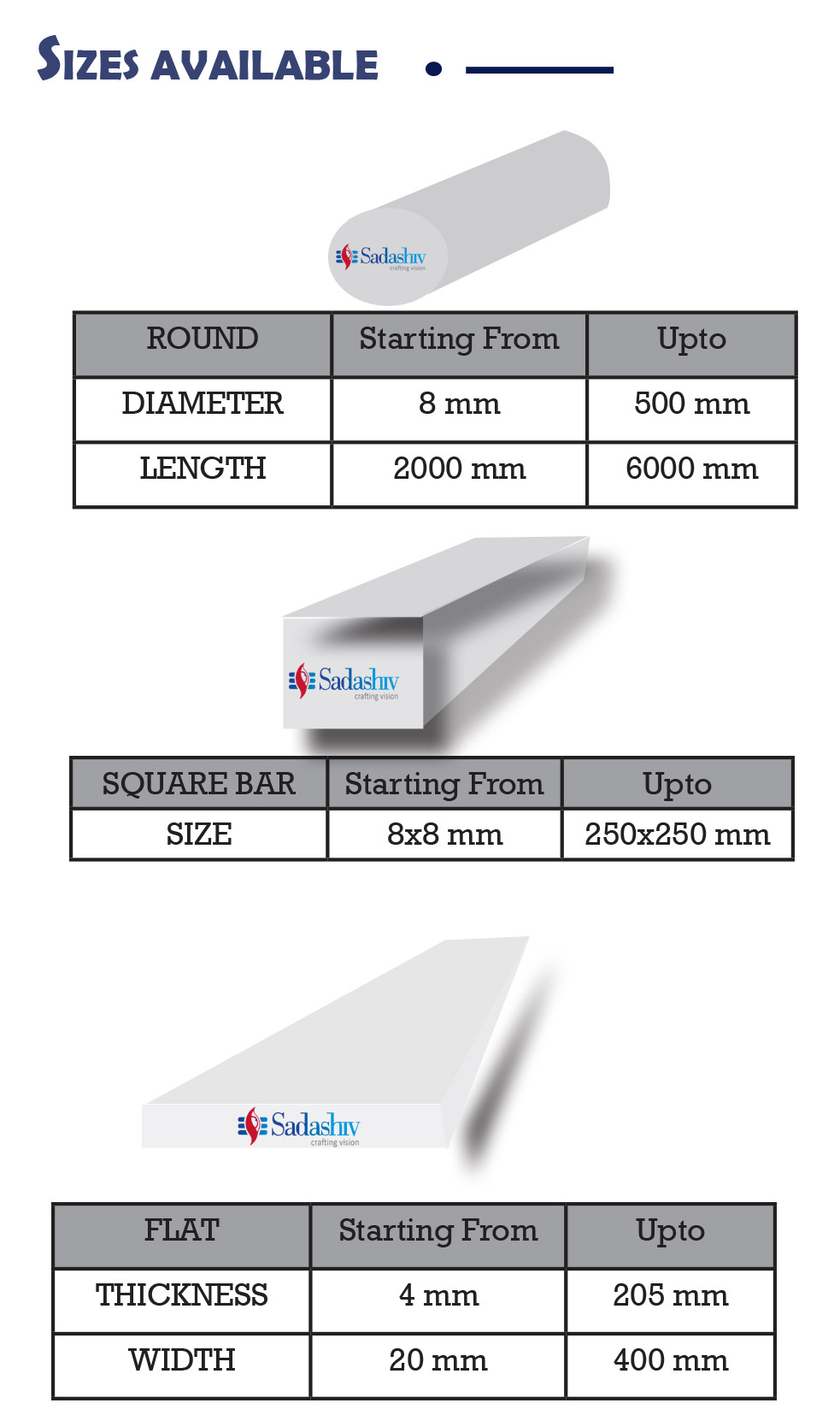
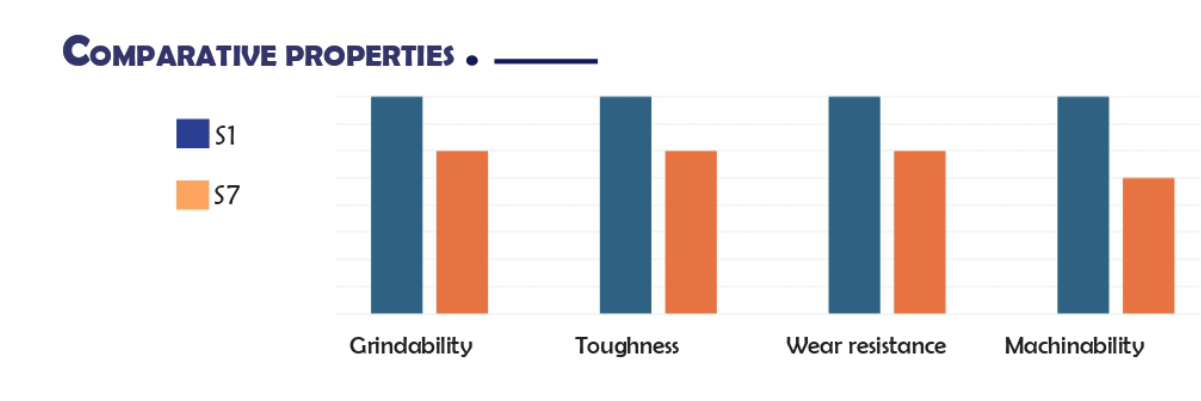